Production of glass micropearl reflecting-film and single-layer coplanar tree
A glass microbead and production process technology, applied in optics, optical components, instruments, etc., can solve the problems of wasting raw materials, affecting reflective brightness, unable to arrange closely, etc., to achieve uniform surface, enhance reflective intensity, and improve appearance. Effect
- Summary
- Abstract
- Description
- Claims
- Application Information
AI Technical Summary
Problems solved by technology
Method used
Image
Examples
Embodiment Construction
[0014] The present invention will be further described below in conjunction with the drawings and embodiments.
[0015] Such as figure 1 As shown, the glass microbeads 1 preheated to 80~90℃ in the oven are put into the fluidized bead tank 2, separated by a gas-permeable plate in the middle. The plates are distributed with uniform pores, and the pore size is smaller than the diameter of the smallest glass bead. . An electrostatic device is used to make the roll of the film take a positive charge, and the glass beads 1 have a negative charge. Hot air at 80° C. is blown from the bottom of the fluidized bead tank 2 to make the glass microbeads adhere to the surface of the adhesive layer 5. After the hot composite steel roller 3 and the rubber roller 4 are pressed together, the hot pressing temperature of the hot composite steel roller 3 is 60~70℃, and the air pressure is controlled at 0.3~0.35MPa, so that the glass beads 1 are evenly and tightly distributed on the surface of the adhe...
PUM
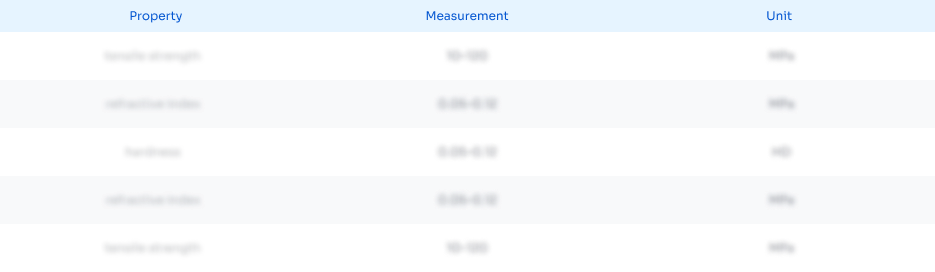
Abstract
Description
Claims
Application Information

- R&D
- Intellectual Property
- Life Sciences
- Materials
- Tech Scout
- Unparalleled Data Quality
- Higher Quality Content
- 60% Fewer Hallucinations
Browse by: Latest US Patents, China's latest patents, Technical Efficacy Thesaurus, Application Domain, Technology Topic, Popular Technical Reports.
© 2025 PatSnap. All rights reserved.Legal|Privacy policy|Modern Slavery Act Transparency Statement|Sitemap|About US| Contact US: help@patsnap.com