Method for combined extracting boron, magnesium and lithium from salt lake bittern
A technology of combined extraction and salt lake brine, applied in the field of magnesium, lithium, and boron joint extraction, can solve the problems of lithium carbonate containing many impurities, low resin utilization rate, high energy consumption, etc., achieve good filtration and washing performance, and save production energy consumption , The effect of small system logistics
- Summary
- Abstract
- Description
- Claims
- Application Information
AI Technical Summary
Problems solved by technology
Method used
Image
Examples
Embodiment 1
[0041] (1) Use brine near saturated magnesium chloride after evaporation and concentration of salt fields to remove most of the sodium and potassium as raw material, wherein the content of diboron trioxide is 2-4%, the concentration of magnesium ions is about 80-120g / L, and the concentration of lithium ions is about 3-4%. 8g / L; purification of raw brine
[0042] (2) With the raw material brine containing boron, magnesium, lithium, remove impurities such as silt and other solid suspended matter by filter press filter, make raw material brine be purified;
[0043] (3) Sulfuric acid or hydrochloric acid method for boric acid
[0044] In an enamel reactor with an effective volume of 10000L, add 9m 3 The purified brine is heated, and when heated to a temperature of 55°C, slowly add 180 L of concentrated sulfuric acid, stirring while adding, and continue stirring for about 1 hour after the addition, and then cooling. When cooled to 15°C, filter and separate with a centrifuge or a ...
Embodiment 2
[0058] (1) Use brine near saturated magnesium chloride after evaporation and concentration of salt fields to remove most of the sodium and potassium as raw material, wherein the content of diboron trioxide is 2-4%, the concentration of magnesium ions is about 80-120g / L, and the concentration of lithium ions is about 3-4%. 8g / L; purification of raw brine
[0059] (2) With the raw material brine containing boron, magnesium, lithium, remove impurities such as silt and other solid suspended matter by filter press filter, make raw material brine be purified;
[0060] (3) Sulfuric acid or hydrochloric acid method for boric acid
[0061] In an enamel reactor with an effective volume of 10000L, add 9m 3 Heating the raw material brine after purification, when the temperature is 60°C, slowly add 1000L concentrated hydrochloric acid, stirring while adding, continue stirring for about 0.5 hours after adding, and then cooling. When cooled to 0°C, use a centrifuge or a filter press to fil...
Embodiment 3
[0075] (1) Use brine near saturated magnesium chloride after evaporation and concentration of salt fields to remove most of the sodium and potassium as raw material, wherein the content of diboron trioxide is 2-4%, the concentration of magnesium ions is about 80-120g / L, and the concentration of lithium ions is about 3-4%. 8g / L; purification of raw brine
[0076] (2) With the raw material brine containing boron, magnesium, lithium, remove impurities such as silt and other solid suspended matter by filter press filter, make raw material brine be purified;
[0077] (3) Sulfuric acid or hydrochloric acid method for boric acid
[0078] In an enamel reactor with an effective volume of 10000L, add 9m 3 Heating the raw material brine after purification, when the temperature is 65°C, slowly add 250L of concentrated sulfuric acid, stirring while adding, continue stirring for about 0.5 hours after adding, and then cooling. When cooled to -5°C, use a centrifuge or a filter press to filter...
PUM
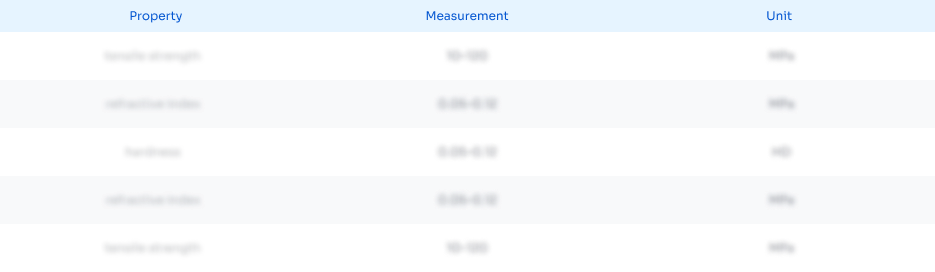
Abstract
Description
Claims
Application Information

- Generate Ideas
- Intellectual Property
- Life Sciences
- Materials
- Tech Scout
- Unparalleled Data Quality
- Higher Quality Content
- 60% Fewer Hallucinations
Browse by: Latest US Patents, China's latest patents, Technical Efficacy Thesaurus, Application Domain, Technology Topic, Popular Technical Reports.
© 2025 PatSnap. All rights reserved.Legal|Privacy policy|Modern Slavery Act Transparency Statement|Sitemap|About US| Contact US: help@patsnap.com