Multilayer ceramic substrate, method for making the same, and composite green sheet for making multilayer ceramic substrate
A technology of multi-layer ceramics and manufacturing methods, applied in the direction of multi-layer circuit manufacturing, etc., can solve the problems of warping of multi-layer ceramic substrates, and the reduction of the effect of restraining the shrinkage of the limiting layer, so as to suppress deformation, reduce dimensional shift, and restrain shrinkage. Effect
- Summary
- Abstract
- Description
- Claims
- Application Information
AI Technical Summary
Problems solved by technology
Method used
Image
Examples
experiment example 1
[0132] In the experimental example, multilayer ceramic substrates of the following samples 1 to 5 were produced.
[0133] (1) Sample 1
[0134] Sample 1 corresponds to an embodiment within the scope of the present invention, and has Figure 14 The raw laminated body 31 of the structure shown was obtained. Figure 14 It is a front view showing the unprocessed laminated body 31 in cross section.
[0135]The unprocessed laminated body 31 includes a base material layer 32, a restriction layer 33, and an intermediate layer 34 in an unprocessed state, and three layers are stacked on each side of the restriction layer 33 of one layer with an intermediate layer 34 interposed therebetween. The structure of the matrix material layer 23. In addition, in the raw laminated body 31 , a plurality of outer conductor films 35 are formed on the upper main surface and a lower main surface, respectively, and a plurality of inner conductor films 36 are formed inside. The internal conductor fil...
experiment example 2
[0177] This experimental example was carried out in order to obtain a desired relationship with respect to each of the thermal expansion coefficients of the base material layer, the constraining layer, and the intermediate layer provided on the multilayer ceramic substrate.
[0178] 1. Production of raw board
[0179] (1) raw board for base material layer
[0180] Precipitated CaO·SiO mixed with an average particle size of 2 μm 3 crystallized glass SiO 2 -CaO-Al 2 o 3 -B 2 o 3 (44:47:5:4) 50 parts by weight of glass-like powder, 50 parts by weight of alumina powder with an average particle diameter of 1.5 μm, 50 parts by weight of water as a dispersant, 20 parts by weight of polyvinyl alcohol as a binder, 1 weight part of polycarbonate-based dispersant as a dispersant is used as a slurry. After removing air bubbles from the slurry, the slurry is formed into a thin plate by a doctor blade method, and dried to obtain a green sheet that should be a base material layer with ...
PUM
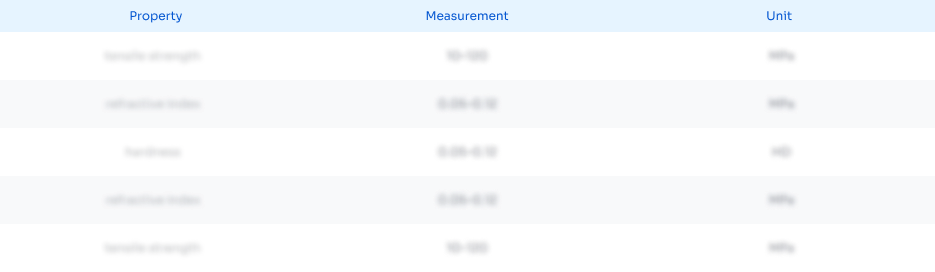
Abstract
Description
Claims
Application Information

- Generate Ideas
- Intellectual Property
- Life Sciences
- Materials
- Tech Scout
- Unparalleled Data Quality
- Higher Quality Content
- 60% Fewer Hallucinations
Browse by: Latest US Patents, China's latest patents, Technical Efficacy Thesaurus, Application Domain, Technology Topic, Popular Technical Reports.
© 2025 PatSnap. All rights reserved.Legal|Privacy policy|Modern Slavery Act Transparency Statement|Sitemap|About US| Contact US: help@patsnap.com