Integral drawn technique for faceplate of buffet dinner stove
A furnace panel and buffet technology, which is applied in the direction of forming tools, manufacturing tools, metal processing equipment, etc., can solve the problems that affect the overall quality and service life of the panel, increase the processing steps of the dining furnace panel, and increase the production cost of the panel, so as to improve the appearance Quality and service life, good price advantage, and the effect of avoiding missing soldering
- Summary
- Abstract
- Description
- Claims
- Application Information
AI Technical Summary
Problems solved by technology
Method used
Image
Examples
Embodiment 1
[0023] Now take 1Cr18Ni9Ti stainless steel as an example to manufacture square buffet stove panels.
[0024] (1) the grade is 3042B, and the stainless steel coil material with a thickness of 1.8mm is cut into 810 × 610 sheets with a plate shear, and the four corners are cut off to form an octagonal sheet;
[0025] (2) Send the corner-cut material into a 315-ton hydraulic press and concave and convex molds for deep drawing, and lay a 2μm polypropylene film between the mold and the workpiece as a lubricant, and the drawing height H is 60-70mm. deep artifacts such as figure 1 shown;
[0026] (3) Use a 160-ton punch to cut off the outer edge of the drawn workpiece;
[0027] (4) Send the sheared workpiece into a 315-ton hydraulic press and a shrinking die to compress the mouth to the required diameter. The die 3 is a barrel cavity with a bell mouth, and the angle between the inner slope of the bell mouth and the inner wall of the barrel is 21° ~ 220 degrees, the positioning mol...
Embodiment 2
[0035] Take the 1Cr18Ni9 stainless steel plate as an example to manufacture the circular panel of the buffet stove.
[0036] (1) Use the φ640 sheet of the stainless steel coil with the grade 2012B and a thickness of 1.8mm, and the shape of the workpiece is as follows Figure 7 shown;
[0037] (2) The circular piece is fed into a 315-ton hydraulic press and concave and convex molds for deep drawing. The lubricant is 1 μm polyethylene film, and the drawing height is 60-65mm. The shape of the workpiece is as follows: Figure 8 shown;
[0038] (3) Place the drawn workpiece in an electric furnace for annealing for 1 hour at an annealing temperature of 1050°C to 1080°C with 99% nitrogen concentration protection;
[0039] (4) Send the annealed workpiece into a 315-ton hydraulic press and concave and convex molds for deep drawing. The lubricant is polyethylene film, and the drawing height is 10-20mm;
[0040] (5) Use a 160-ton punch to cut off the outer edge of the workpiece that h...
PUM
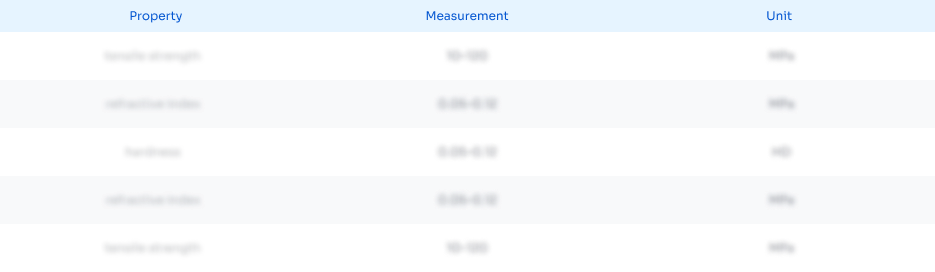
Abstract
Description
Claims
Application Information

- R&D
- Intellectual Property
- Life Sciences
- Materials
- Tech Scout
- Unparalleled Data Quality
- Higher Quality Content
- 60% Fewer Hallucinations
Browse by: Latest US Patents, China's latest patents, Technical Efficacy Thesaurus, Application Domain, Technology Topic, Popular Technical Reports.
© 2025 PatSnap. All rights reserved.Legal|Privacy policy|Modern Slavery Act Transparency Statement|Sitemap|About US| Contact US: help@patsnap.com