A serum casting and pulping method and pulping equipment thereof
A slurry and pulping technology, used in clay processing equipment, clay preparation devices, chemical instruments and methods, etc., can solve the problems of large floor space, shortened time, large investment, etc., to improve production capacity, improve utilization rate, use handy effect
- Summary
- Abstract
- Description
- Claims
- Application Information
AI Technical Summary
Problems solved by technology
Method used
Image
Examples
Embodiment 1
[0026] First prepare the fly ash slurry containing gypsum powder with a water-to-material ratio of 0.53 and add it to the pouring mixer, then prepare the lime cement slurry with a water-to-material ratio of 0.75 and add it to the pouring mixer; then add the foaming agent aluminum powder slurry and pass the heating steam into the In the casting mixer, after mixing and stirring, it takes 3 minutes to prepare a fully mixed and dispersed casting slurry. The weight ratio of raw materials: fly ash: cement: lime: gypsum = 75: 4: 16: 4; compared with the old process, the fly ash increased by 5%, the lime decreased by 5%, and the others were the same as the old process.
[0027] 190 seconds per pouring unit time. The timing arrangement is as follows: from 0 to 40 seconds, add fly ash slurry; from 5 to 45 seconds, add cement lime slurry; from 85 to 100 seconds, add foaming agent aluminum powder slurry; from 80 seconds to 140 seconds, add steam adjustment Adjust the slump by temperature...
Embodiment 2
[0034] Slurry pouring equipment adopts pouring mixer and figure 2 The calcium raw material pulping machine is composed of two parts, and the calcium raw material pulping machine is arranged above the pouring mixer.
[0035] The calcareous raw material pulping machine may use a valve 7, an agitator 12 for preparing calcareous slurry, a calcareous powder screw conveyor 13, a calcareous powder blanking port 14, and a water adding metering tank 15. Valve 7 is installed on the water inlet pipeline of adding water metering tank 15 below. The water inlet pipe mouth and the calcareous powder screw conveyor 13 are installed above the agitator 12 for preparing the calcareous slurry, and the agitator 12 for preparing the calcareous slurry is installed above the slurry addition port 5 of the calcareous raw material of the pouring mixer, and the calcium The powder feeding port 14 is arranged on the front end of the calcareous powder screw conveyor 13 .
[0036] 200 seconds per cast unit...
Embodiment 3
[0040] The slurry pouring equipment consists of two parts: a pouring mixer and a calcareous raw material pulping machine, and the calcareous raw material pulping machine is arranged above the pouring mixer.
[0041] Silicon raw material: SiO 2 Tailings sand with a content of 85%, 0.08 sieve 20%-28%, water-to-material ratio 0.5; calcium raw material adopts medium-speed quicklime with CaO content of 85%, 0.08 sieve 15%-20%, 425# cement, gypsum, aluminum Powder cream.
[0042] The amount of dry materials per pouring unit: tailings sand 1800Kg, waste blocks 70-90Kg, gypsum 90Kg; lime 280Kg, cement 280Kg, aluminum powder paste 2Kg.
[0043] In the first step of the work, the tailings sand is wet ball milled into a slurry, and the water-material ratio is 0.5, which is measured according to the amount of each pouring unit; lime, gypsum, and waste blocks are ground into mixed powder according to the weight ratio, and lime, Gypsum and waste block mixed powder are made into slurry acc...
PUM
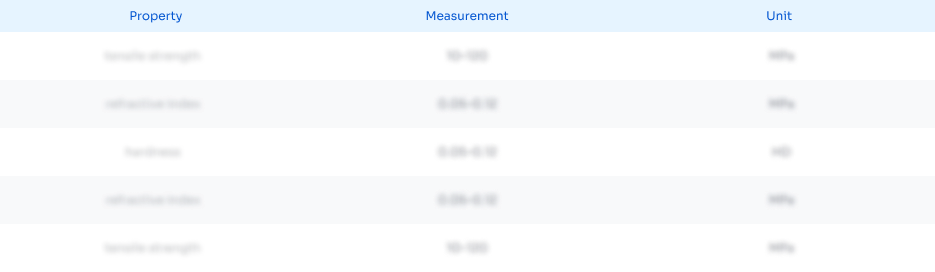
Abstract
Description
Claims
Application Information

- Generate Ideas
- Intellectual Property
- Life Sciences
- Materials
- Tech Scout
- Unparalleled Data Quality
- Higher Quality Content
- 60% Fewer Hallucinations
Browse by: Latest US Patents, China's latest patents, Technical Efficacy Thesaurus, Application Domain, Technology Topic, Popular Technical Reports.
© 2025 PatSnap. All rights reserved.Legal|Privacy policy|Modern Slavery Act Transparency Statement|Sitemap|About US| Contact US: help@patsnap.com