Full automatic compounding process and mould for household motor shell
A technology of motor casing and composite mold, which is applied in the manufacture of electric generators, forming tools, manufacturing tools, etc., can solve the problems of increasing machine investment costs and maintenance costs, low work efficiency, and hidden dangers to personal safety, and achieve excellent process design , Improve productivity, and prevent work-related accidents
- Summary
- Abstract
- Description
- Claims
- Application Information
AI Technical Summary
Problems solved by technology
Method used
Image
Examples
Embodiment Construction
[0019] See Fig. 1 and Fig. 2, the tooling equipment of this example is that the upper mold base includes upper template 1, which is fixed on the punch of the stamping machine tool, and upper template 2 2 is fixedly connected under the symmetry of upper template 1, and the upper template The lower part of the second 2 is provided with a reinforcing plate 4, and 7 support plates 5 are uniformly arranged in the middle; the upper template 3 3 is connected under the reinforcing plate 4 and the supporting plate 5, and the mold fixing plate 7 is connected under the front end of the upper template 3 3 , a mold fixing plate 28 is connected below the rear end of the upper template 3, and four square holes are sequentially arranged on the upper template three 3: 46A, 46B, 46C and 46D are symmetrically connected with punches 18A, 18B, 18C, 18D, There are six round holes: 45A, 45B, 45C, 45D, 45E, and 45F are tightly matched with six symmetrical guide bushes 6; The lower mold fixing plate A...
PUM
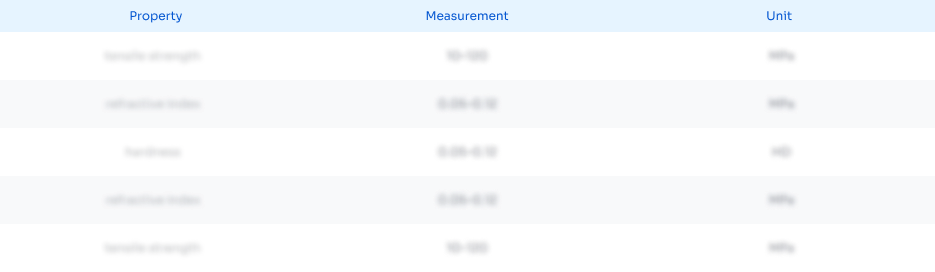
Abstract
Description
Claims
Application Information

- R&D
- Intellectual Property
- Life Sciences
- Materials
- Tech Scout
- Unparalleled Data Quality
- Higher Quality Content
- 60% Fewer Hallucinations
Browse by: Latest US Patents, China's latest patents, Technical Efficacy Thesaurus, Application Domain, Technology Topic, Popular Technical Reports.
© 2025 PatSnap. All rights reserved.Legal|Privacy policy|Modern Slavery Act Transparency Statement|Sitemap|About US| Contact US: help@patsnap.com