Fabric product finishing agent and its preparing process and method thereof
A technology for textile finishing and preparation technology, applied in the fields of physical technology, textile technology, and chemical technology, it can solve the problems of single function, difficult-to-function organic compounds, and organic materials are harmful to human health, etc., and achieves simple process, easy procurement, and investment. less effect
- Summary
- Abstract
- Description
- Claims
- Application Information
AI Technical Summary
Problems solved by technology
Method used
Examples
Embodiment 1
[0024] Example 1: Using butyl titanate and zinc acetate as precursors, glacial acetic acid as a catalyst and peptizer, water as a solvent, absolute ethanol as a solvent for butyl titanate, ethanolamine as a precipitant and provides OH - , silver nitrate provides Ag + , TiO formed by hydrolysis and polycondensation reaction 2 / ZnO and doped with Ag + Nano sol finishing agent, its composition and weight content are as follows: 0.1 g of butyl titanate, 0.1 g of zinc acetate dihydrate, 1 g of absolute ethanol, 5 g of glacial acetic acid, 0.1 g of ethanolamine, and 0.1 g of silver nitrate 0.005 grams of water with a balance of 93.695 grams.
[0025] Its production process is as follows:
[0026] 1) 0.1 gram of zinc acetate dihydrate, 0.005 gram of silver nitrate, 0.33 gram of dehydrated alcohol and 93.695 grams of water of 1 / 3 amount are mixed, and the rotating speed is that the magnetic stirrer of 1600 rev / min stirs for a period of time to form uniform, Transparent A solution,...
Embodiment 2
[0033] Example 2: Using butyl titanate and zinc acetate as precursors, glacial acetic acid as a catalyst and peptizer, water as a solvent, absolute ethanol as a solvent for butyl titanate, ethanolamine as a precipitant and provides OH - , silver nitrate provides Ag + , TiO formed by hydrolysis and polycondensation reaction 2 / ZnO and doped with Ag + Nano sol finishing agent, its composition and weight content are as follows: 15 grams of butyl titanate, 12 grams of zinc acetate dihydrate, 20 grams of absolute ethanol, 15 grams of glacial acetic acid, 5 grams of ethanolamine, and 5 grams of silver nitrate 0.2 grams of water with a balance of 32.8 grams.
[0034] Its production process is as follows:
[0035] 1) 12 grams of zinc acetate dihydrate, 0.2 gram of silver nitrate, 6.67 grams of dehydrated alcohol and 32.8 grams of water of 1 / 3 amount are mixed, and the rotating speed is to form uniform, Transparent A solution, operate at a temperature below 20°C.
[0036] 2) Stir ...
Embodiment 3
[0042] Example 3: Using butyl titanate and zinc acetate as precursors, glacial acetic acid as catalyst and peptizer, water as solvent, absolute ethanol as the solvent of butyl titanate, ethanolamine as precipitant and provides OH - , silver nitrate provides Ag + , TiO formed by hydrolysis and polycondensation reaction 2 / ZnO and doped with Ag + Nano sol finishing agent, its composition and weight content are as follows: 8.22 grams of butyl titanate, 5.31 grams of zinc acetate dihydrate, 10 grams of absolute ethanol, 9.67 grams of glacial acetic acid, 1.47 grams of ethanolamine, and 1.47 grams of silver nitrate 0.07 g, with a balance of 65.26 g of water.
[0043] 1) 5.31 grams of zinc acetate dihydrate, 0.07 grams of silver nitrate, 3.34 grams of dehydrated alcohol of 1 / 3 amount and 65.26 grams of water are mixed, and the rotating speed is to form uniform, Transparent A solution, operate at a temperature below 20°C.
[0044] 2) Stir 8.22 grams of butyl titanate, the balance...
PUM
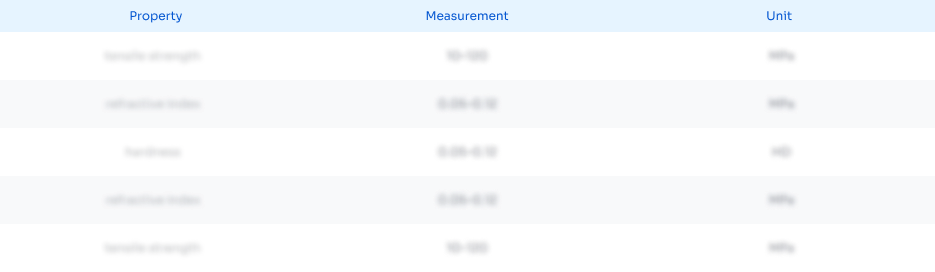
Abstract
Description
Claims
Application Information

- R&D
- Intellectual Property
- Life Sciences
- Materials
- Tech Scout
- Unparalleled Data Quality
- Higher Quality Content
- 60% Fewer Hallucinations
Browse by: Latest US Patents, China's latest patents, Technical Efficacy Thesaurus, Application Domain, Technology Topic, Popular Technical Reports.
© 2025 PatSnap. All rights reserved.Legal|Privacy policy|Modern Slavery Act Transparency Statement|Sitemap|About US| Contact US: help@patsnap.com