Porosity aperture controllable magnesium foam material and preparation method thereof
A foam material and porosity technology, which is applied in the field of magnesium foam materials with controllable porosity and pore size and their preparation, can solve the problems of inability to produce magnesium foam materials, and achieve the purpose of preventing delamination, reducing scrap rate, and high energy absorption. performance effect
- Summary
- Abstract
- Description
- Claims
- Application Information
AI Technical Summary
Problems solved by technology
Method used
Image
Examples
Embodiment 1
[0013] Example 1: 1) After mixing magnesium powder, spherical urea particles with a size in the order of millimeters, and additive ethanol uniformly, they are placed in a mold with a desired shape and subjected to a unidirectional pressure of 300 MPa to obtain a green body; wherein, The mass of magnesium powder and urea granules is determined by the formula m 镁 =V×(1-P)×1.74, m 尿素 =V×P×1.335, where V is the volume of the magnesium foam, P is the porosity (50%), 1.74 and 1.335 are the density of magnesium powder and urea in the dense state, and the amount of additive ethanol added It is 1% of the total mass of magnesium powder and urea. 2) Soak the green body in an aqueous sodium hydroxide solution with a concentration of 0.0005 mol / L for 5 hours. 3). Put the soaked green body in an argon atmosphere at 240°C for 5 hours, and then place it at 610°C for 4.5 hours, or first place the soaked green body under vacuum (the degree of vacuum is ≤10 -4 Pa) in 240 ℃ for 5 hours, and then plac...
Embodiment 2
[0014] Example 2: 1) After mixing magnesium powder, spherical urea particles with a size in the order of millimeters, and additive ethanol uniformly, they are placed in a mold with a desired shape and subjected to unidirectional pressure at 325 MPa to obtain a green body; wherein, The mass of magnesium powder and urea granules is determined by the formula m 镁 =V×(1-P)×1.74, m 尿素 =V×P×1.335, where V is the volume of the magnesium foam, P is the porosity (currently selected as 60%), 1.74 and 1.335 are the density of magnesium powder and urea in the dense state, and the amount of additive ethanol added It is 2% of the total mass of magnesium powder and urea. 2) Soak the green body in an aqueous sodium hydroxide solution with a concentration of 0.00075 mol / L for 3 hours. 3). Put the soaked green body in an argon atmosphere at 245°C for 4.5 hours, and then place it at 615°C for 4 hours, or first place the soaked green body under vacuum (the degree of vacuum is ≤10 -4 Pa) in 245 ℃ for 4...
Embodiment 3
[0015] Example 3: 1) After mixing magnesium powder, spherical urea particles with a size in the order of millimeters, and additive ethanol uniformly, they are placed in a mold of a desired shape and subjected to unidirectional pressure 350MPa to obtain a green body; wherein, The mass of magnesium powder and urea granules is determined by the formula m 镁 =V×(1-P)×1.74, m 尿素 =V×P×1.335, where V is the volume of magnesium foam, P is the porosity (70%), 1.74 and 1.335 are the density of magnesium powder and urea in the dense state, and the amount of additive ethanol added It is 3% of the total mass of magnesium powder and urea. 2) The green body is immersed in a sodium hydroxide aqueous solution with a concentration of 0.001 mol / L for 1.5 hours. 3). Put the soaked green body in an argon atmosphere at 250°C for 4 hours, and then place it at 620°C for 3.5 hours, or first place the soaked green body under vacuum (the degree of vacuum is ≤10 -4 Pa) in 250 ℃ for 4 hours, and then placed at...
PUM
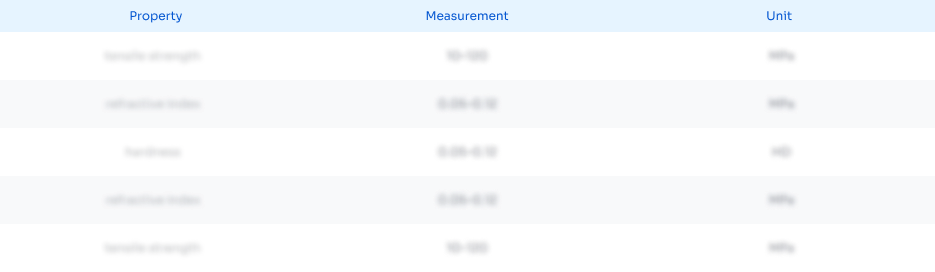
Abstract
Description
Claims
Application Information

- Generate Ideas
- Intellectual Property
- Life Sciences
- Materials
- Tech Scout
- Unparalleled Data Quality
- Higher Quality Content
- 60% Fewer Hallucinations
Browse by: Latest US Patents, China's latest patents, Technical Efficacy Thesaurus, Application Domain, Technology Topic, Popular Technical Reports.
© 2025 PatSnap. All rights reserved.Legal|Privacy policy|Modern Slavery Act Transparency Statement|Sitemap|About US| Contact US: help@patsnap.com