Assitants for catalyzing cyacking of reducing gasoline sulphur content, preparation process and application thereof
A technology of catalytic cracking additives and sulfur content, which is applied in catalytic cracking, chemical instruments and methods, physical/chemical process catalysts, etc., and can solve problems such as reducing gasoline sulfur content
- Summary
- Abstract
- Description
- Claims
- Application Information
AI Technical Summary
Problems solved by technology
Method used
Examples
Embodiment 1
[0036] 10Kg (dry basis) of hydrated kaolin was added with water to make a slurry with a solid content of 35%, and 0.53Kg of sodium silicate was added as a dispersant for spray molding to obtain 8.5Kg of spray microspheres. The sprayed microspheres were calcined in a muffle furnace at 940° C. for 3 h to obtain the calcined microspheres. In a stirring state, 5 L of deionized water and 1000 g of roasted microspheres were successively put into a stainless steel reactor, 300 g of sodium hydroxide was added, the temperature was raised to 90° C. and kept at a constant temperature for 3 h, filtered and washed to obtain a filter cake. While stirring, put 5 L of deionized water and the above filter cake into the stainless steel reactor successively, add 200 ml of 36.5% hydrochloric acid and 100 g of ammonium chloride, raise the temperature to 90° C. and keep the temperature constant for 0.5 h. Sodium oxide content in the microsphere obtained after treatment is 0.60%, zinc nitrate 22g, g...
Embodiment 2
[0038] 10Kg (thousand bases) hydrated kaolin is added with water to make a slurry with a solid content of 20%, and 0.2Kg sodium hydroxide, 0.2Kg sodium pyrophosphate, and 0.1Kg sodium hexametaphosphate are added as a dispersant, and sprayed into microspheres to obtain 8Kg of spray microspheres. The sprayed microspheres were calcined in a muffle furnace at 1000°C for 1 h to obtain the calcined microspheres. Under stirring, 5 L of deionized water and 1000 g of roasted microspheres were successively put into a stainless steel reactor, 500 g of potassium hydroxide was added, the temperature was raised to 90° C. and kept at a constant temperature for 2 h, filtered and washed to obtain a filter cake. In a stirring state, 5 L of deionized water and the above filter cake were successively put into a stainless steel reactor, 200 g of acetic acid and 100 g of ammonium sulfate were added, and the temperature was raised to 90° C. and kept at a constant temperature for 1 h. The content of...
Embodiment 3
[0040] The sprayed microspheres obtained in Example 1 were calcined in a muffle furnace at 750° C. for 3 h to obtain calcined microspheres. Under stirring, 1 L of deionized water and 1000 g of roasted microspheres were successively put into a stainless steel reactor, 4 L of 1M sulfuric acid was added, the temperature was raised to 90° C. and kept at a constant temperature for 1 h, filtered and washed to obtain a filter cake. The content of sodium oxide in the filter cake microspheres obtained after treatment is 0.20%, and then 600g of the microspheres, 24g of nickel nitrate, 20g of copper nitrate, 10g of titanium sulfate, and 2000ml of deionized water are put into a stainless steel reactor at a constant temperature of 90°C. Exchanging for 1h, the auxiliary agent C of the present invention was obtained.
PUM
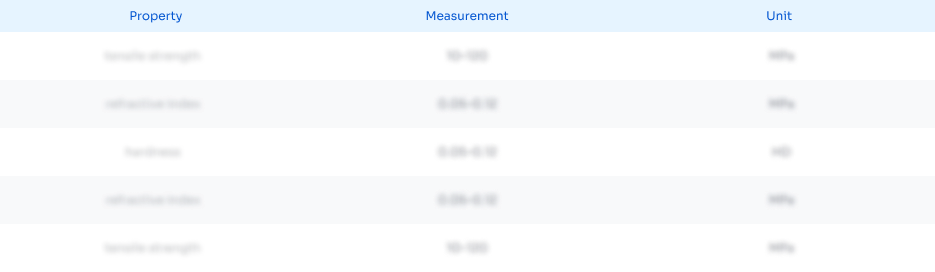
Abstract
Description
Claims
Application Information

- R&D
- Intellectual Property
- Life Sciences
- Materials
- Tech Scout
- Unparalleled Data Quality
- Higher Quality Content
- 60% Fewer Hallucinations
Browse by: Latest US Patents, China's latest patents, Technical Efficacy Thesaurus, Application Domain, Technology Topic, Popular Technical Reports.
© 2025 PatSnap. All rights reserved.Legal|Privacy policy|Modern Slavery Act Transparency Statement|Sitemap|About US| Contact US: help@patsnap.com