Continuous manufacture method for antiskid foamed material with stereo burr
A technology of foaming material and manufacturing method, which is applied in the field of plastic molding, can solve the problems of loss of characteristics, damping characteristics and anti-slip effect reduction, etc., and achieve the effect of improving use performance, good damping characteristics and anti-slip effect, and continuous production
- Summary
- Abstract
- Description
- Claims
- Application Information
AI Technical Summary
Problems solved by technology
Method used
Image
Examples
Embodiment Construction
[0022] The present invention uses a kind of thermoplastic elastomer colloid to replace the traditional rubber raw material, to make use of the characteristics that the thermoplastic elastomer colloid is easy to heat and form in the foaming process, and to produce a three-dimensional embossed pattern as shown in Figure 4 Anti-slip foam material 50.
[0023] The present invention comprises the steps:
[0024] step one
[0025] Making foam material body embryo
[0026] First put the thermoplastic elastomer granules into the mold and perform foaming operation to make the foam material embryo.
[0027] step two
[0028] Cutting to form a single piece of foam material
[0029] As shown in Figure 1, the foaming material body blank is taken out from the mold, and it is removed and trimmed to form a cubic foaming material 10 as shown in Figure 1, and the thickness can be made according to the actual demand. The foam material 10 is cut into several foam material single sheets 20 . ...
PUM
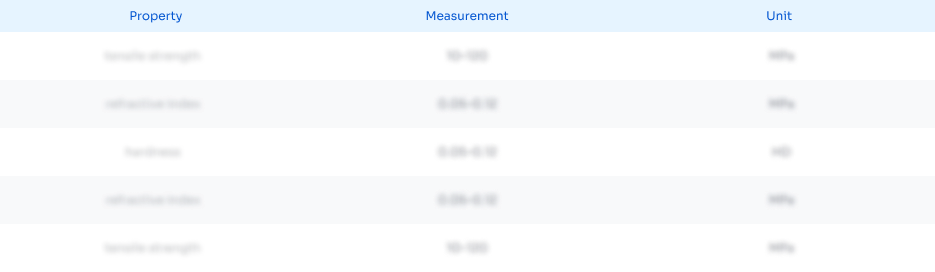
Abstract
Description
Claims
Application Information

- R&D
- Intellectual Property
- Life Sciences
- Materials
- Tech Scout
- Unparalleled Data Quality
- Higher Quality Content
- 60% Fewer Hallucinations
Browse by: Latest US Patents, China's latest patents, Technical Efficacy Thesaurus, Application Domain, Technology Topic, Popular Technical Reports.
© 2025 PatSnap. All rights reserved.Legal|Privacy policy|Modern Slavery Act Transparency Statement|Sitemap|About US| Contact US: help@patsnap.com