Galvanized steel sheet coating material and its production method
A technology of galvanized steel sheet and production method, applied in the direction of metal material coating process, coating, etc., can solve the problems of cracking, poor corrosion resistance, coating peeling, etc.
- Summary
- Abstract
- Description
- Claims
- Application Information
AI Technical Summary
Problems solved by technology
Method used
Examples
Embodiment 1
[0012] Formula: aluminum Al50%, zinc Zn47%, silicon SI2.8%, rare earth Re0.2%. When feeding, first add aluminum Al, then heat up to 800°C, add silicon Si, and stir evenly, then heat up to 850°C, add rare earth Re, stir evenly, then heat up to 880°C, add zinc Zn, stir well Set aside for 35 minutes, then refining, degassing, heat preservation at 780°C, and casting into ingots. The method of re-refining and degassing is the same as above.
Embodiment 2
[0014] Formula: aluminum Al60%, zinc Zn38%, silicon Si1.9%, rare earth Re0.1%. When feeding, first add aluminum Al, then heat up to 800°C, add silicon Si, and stir evenly, then heat up to 850°C, add rare earth Re, stir evenly, then heat up to 860°C, add zinc Zn, stir well Set aside for 30 minutes, then refining, degassing, heat preservation at 760°C, and casting into ingots. The method of re-refining and degassing is the same as above.
Embodiment 3
[0016] Formula: aluminum Al55.4%, zinc Zn44%, silicon Si0.5%, rare earth Re0.1%. When feeding, first add aluminum Al, then heat up to 800°C, add silicon Si, and stir evenly, then raise the temperature to 850°C, add rare earth Re, stir evenly, then heat up to 860°C-880°C, then add zinc Zn, After stirring evenly, place it for 30-35 minutes, then refine, degas, keep warm at 760°C-780°C, and cast into ingots. The method of re-refining and degassing is the same as above.
PUM
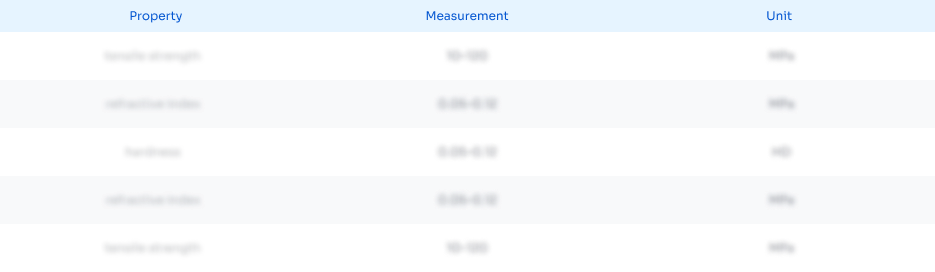
Abstract
Description
Claims
Application Information

- Generate Ideas
- Intellectual Property
- Life Sciences
- Materials
- Tech Scout
- Unparalleled Data Quality
- Higher Quality Content
- 60% Fewer Hallucinations
Browse by: Latest US Patents, China's latest patents, Technical Efficacy Thesaurus, Application Domain, Technology Topic, Popular Technical Reports.
© 2025 PatSnap. All rights reserved.Legal|Privacy policy|Modern Slavery Act Transparency Statement|Sitemap|About US| Contact US: help@patsnap.com