Method for preparing microlite silicon
A technology of microcrystalline silicon and amorphous silicon thin film, applied in the field of silicon materials, transforming amorphous silicon into microcrystalline silicon, can solve the problems of reducing manufacturing costs, low mobility, low crystallinity, etc.
- Summary
- Abstract
- Description
- Claims
- Application Information
AI Technical Summary
Problems solved by technology
Method used
Image
Examples
Embodiment Construction
[0019] The present invention will be further described below in combination with specific embodiments.
[0020] A 50nm-thick hydrogenated amorphous silicon film (a-Si:H) was deposited on glass by plasma-enhanced chemical vapor deposition (PECVD), the substrate temperature was 220°C, and the RF power density was 0.03W / cm 2 , the gas flow rate is 15 sccm, and the reaction chamber pressure is 80Pa.
[0021] The above-mentioned hydrogenated amorphous silicon film sample 6 is placed upward on the heating plate 2 at the bottom of the vacuum annealing furnace 1 shown in Figure 1, and after the window 5 is covered, the annealing furnace is evacuated; when the vacuum reaches 2Pa, the heating plate 2 is turned on. The power supply is heated, and the ultraviolet light source 4 is turned on at the same time; when the sample 6 reaches the set temperature of 400°C, the ultraviolet illuminance of the ultraviolet light source 4 is stabilized at 1mW / cm 2 , remove the cover on the window 5, le...
PUM
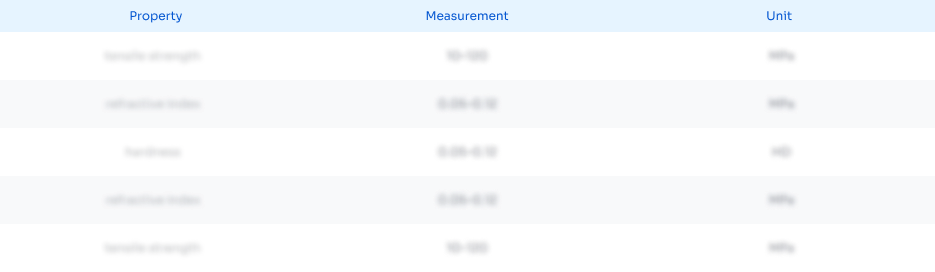
Abstract
Description
Claims
Application Information

- R&D Engineer
- R&D Manager
- IP Professional
- Industry Leading Data Capabilities
- Powerful AI technology
- Patent DNA Extraction
Browse by: Latest US Patents, China's latest patents, Technical Efficacy Thesaurus, Application Domain, Technology Topic, Popular Technical Reports.
© 2024 PatSnap. All rights reserved.Legal|Privacy policy|Modern Slavery Act Transparency Statement|Sitemap|About US| Contact US: help@patsnap.com