Accumulating fuel injection apparatus
a fuel injection apparatus and accumulator technology, applied in the direction of fuel injecting pumps, machines/engines, electric control, etc., can solve the problems of increasing smoke, inability to use this injector, and not achieving atomization of fuel, so as to reduce the fuel pressure, increase the opening area, and reduce the effect of fuel pressur
- Summary
- Abstract
- Description
- Claims
- Application Information
AI Technical Summary
Benefits of technology
Problems solved by technology
Method used
Image
Examples
first embodiment
The embodiments of the accumulating fuel injection apparatus according to the present invention will now be described with reference to the drawings. the accumulating fuel injection apparatus according to the present invention will now be described with reference to FIGS. 1 and 2.
As shown in FIG. 1, a casing 2 for an injector 1 is provided therein with a guide bore 3, a fuel storage chamber 4, and a control volume, i.e. a balancing chamber 5. A needle valve 6 is provided slidably in the guide bore 3. The needle valve 6 comprises a larger-diameter portion 7 fitted slidably in the guide bore 3, and a smaller-diameter portion 8 made integral with the larger-diameter portion 7. The larger-diameter portion 7 of the needle valve 6 is provided with a slit 10 communicating the balancing chamber 5 and fuel storage chamber 4 with each other and extending axially. The slit 10 faces the interior of the balancing chamber 5 with the needle valve closed, with an opening area corresponding to a hei...
third embodiment
The third embodiment shown in FIG. 4 of the accumulating fuel injection apparatus according to the present invention is provided with a restriction 57 in a fuel supply passage extending from a fuel supply port 19 to an injection nozzle 11, i.e. an annular supply passage formed between a smaller-diameter portion of a needle valve and the portion of an inner surface of a casing which is around the smaller-diameter portion. Owing to this arrangement, when a fuel flows in the fuel supply passage extending from the fuel supply port 19 to the injection nozzle 11, a pressure drop occurs in the fuel in the restriction 57, and the resultant pressure works on a seat 15, so that a force imparted to a needle valve 6 in the valve opening direction becomes smaller. Therefore, when the fuel pressure in a balancing chamber 5 decreases momentarily by an operation of a valve 22, the needle valve 6 can be closed reliably on the basis of a differential pressure working thereon. Since the constituent el...
PUM
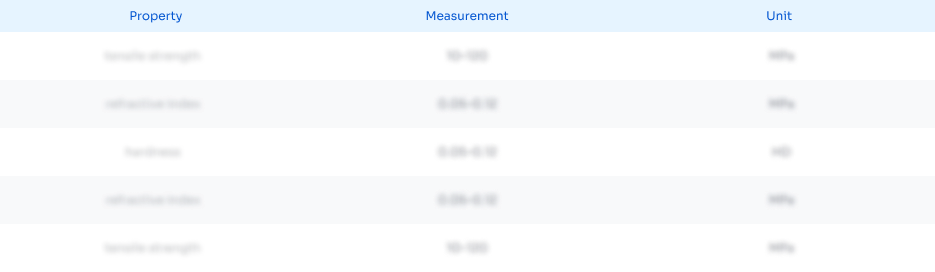
Abstract
Description
Claims
Application Information

- R&D
- Intellectual Property
- Life Sciences
- Materials
- Tech Scout
- Unparalleled Data Quality
- Higher Quality Content
- 60% Fewer Hallucinations
Browse by: Latest US Patents, China's latest patents, Technical Efficacy Thesaurus, Application Domain, Technology Topic, Popular Technical Reports.
© 2025 PatSnap. All rights reserved.Legal|Privacy policy|Modern Slavery Act Transparency Statement|Sitemap|About US| Contact US: help@patsnap.com