Combined cycle with steam cooled gas turbine
- Summary
- Abstract
- Description
- Claims
- Application Information
AI Technical Summary
Benefits of technology
Problems solved by technology
Method used
Image
Examples
Embodiment Construction
With reference to FIGS. 1A and 1B, the invention is incorporated in a multi-pressure reheat combined cycle power generation system 10. In the preferred embodiment, there is included a gas turbine system 12 comprising a compressor 18, a combustion system 16 and a gas turbine 14. A steam turbine system 20 includes a high pressure section 22, an intermediate pressure section 24 and one or more low pressure sections 26 with multiple steam admission points at different pressures. The low pressure section 26 exhausts to a condenser 28. The steam turbine drives the generator 30 which produces electrical power. The gas turbine 12, steam turbine 20 and generator 30 are arranged in tandem on a single shaft 32.
The combined cycle system as described herein includes a multi-pressure HRSG 36 which includes a low pressure (LP) economizer 38, an LP evaporator 40, an HP and IP economizer 42, a low pressure superheater 44, an IP evaporator 46, an HP economizer 48, an HP evaporator 50, a first HP supe...
PUM
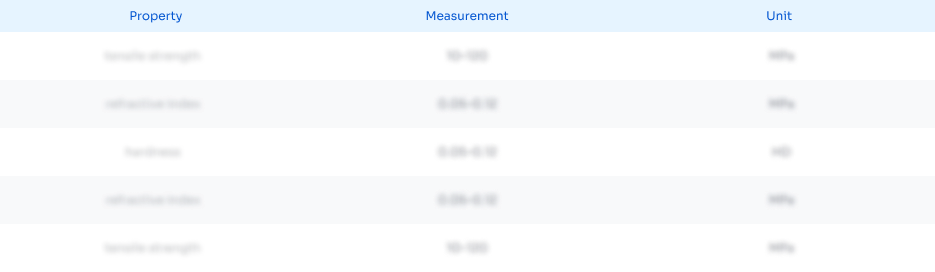
Abstract
Description
Claims
Application Information

- R&D
- Intellectual Property
- Life Sciences
- Materials
- Tech Scout
- Unparalleled Data Quality
- Higher Quality Content
- 60% Fewer Hallucinations
Browse by: Latest US Patents, China's latest patents, Technical Efficacy Thesaurus, Application Domain, Technology Topic, Popular Technical Reports.
© 2025 PatSnap. All rights reserved.Legal|Privacy policy|Modern Slavery Act Transparency Statement|Sitemap|About US| Contact US: help@patsnap.com