Rotorcraft skid undercarriage and a rotorcraft including such an undercarriage
a technology of rotorcraft and undercarriage, which is applied in the direction of rotocraft, aircraft components, and landing gear, etc., can solve the problems of explosive coupling, skid undercarriage, and relatively complex and heavy undercarriage described in those documents, so as to reduce the (angular) stiffness of the aircraft roll, increase the deformation capacity, and reduce the effect of angular stiffness
- Summary
- Abstract
- Description
- Claims
- Application Information
AI Technical Summary
Benefits of technology
Problems solved by technology
Method used
Image
Examples
Embodiment Construction
[0041]With reference to FIG. 1 in particular, the present invention applies specifically to a skid undercarriage 20 fitted to a helicopter 21 whose airframe 22 can rest on the ground 23 via an undercarriage.
[0042]In the meaning of the present application, the term “skid undercarriage” designates an undercarriage comprising two skids, skis, or floats given overall references 24 and 29 and that extend substantially along the longitudinal axis 51 of the rotorcraft.
[0043]The skids 24 and 25 are connected together by a front cross-member 26 and by a rear cross-member 27, each of these cross-members presenting two downwardly-curved end portions. Each outer or lateral end of the cross-members is connected to one of the skids.
[0044]With reference to FIGS. 1 and 2, the rear cross-member 27 receives single connection means 28 for connection with the fuselage (airframe) of the helicopter, in a bearing zone or point located in the middle of the cross-member 27.
[0045]The front cross-member 26 re...
PUM
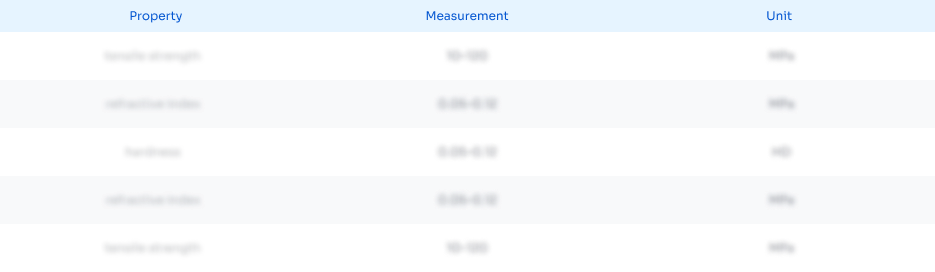
Abstract
Description
Claims
Application Information

- R&D
- Intellectual Property
- Life Sciences
- Materials
- Tech Scout
- Unparalleled Data Quality
- Higher Quality Content
- 60% Fewer Hallucinations
Browse by: Latest US Patents, China's latest patents, Technical Efficacy Thesaurus, Application Domain, Technology Topic, Popular Technical Reports.
© 2025 PatSnap. All rights reserved.Legal|Privacy policy|Modern Slavery Act Transparency Statement|Sitemap|About US| Contact US: help@patsnap.com