Multiphase motors with single point sensing based commutation
a multi-phase motor and sensing technology, applied in the direction of electronic commutators, motor/generator/converter stoppers, dynamo-electric converter control, etc., can solve the problems of unreliable motor performance, simple, unreliable time domain-based multi-phase switching, etc., and achieve reliable motor performance.
- Summary
- Abstract
- Description
- Claims
- Application Information
AI Technical Summary
Benefits of technology
Problems solved by technology
Method used
Image
Examples
Embodiment Construction
[0103]Referring to FIGS. 1 and 2, a multiphase D.C. PM motor incorporating the single sensor based control features of the invention is revealed in general at 10. As noted earlier, the term “multiphase” as used herein is intended to mean three or more phases. Such motors are further characterized in that the number of rotor poles will be different than the number of stator poles. Motor 10 is seen in FIG. 1 to be formed with an aluminum base 12 disposed symmetrically about a rotor axis 14 and having a circular flange represented in general at 16, the circular edge 18 of which carries a connecting groove 20 employed for mounting motor 10 within an appliance. Supported upon the annular rearward surface 22 of flange 16, as well as in conjunction with a recessed cylindrical based shoulder portion 24 is a pressed powdered metal stator core assembly represented generally at 26. The six pole, integrally formed stator core assembly 26, as represented in FIG. 2, is seen to incorporate spaced ...
PUM
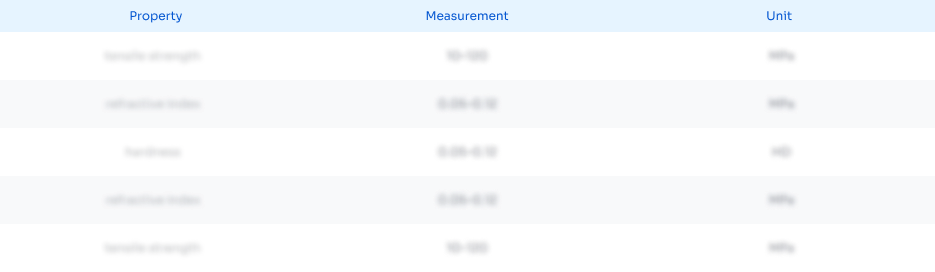
Abstract
Description
Claims
Application Information

- R&D
- Intellectual Property
- Life Sciences
- Materials
- Tech Scout
- Unparalleled Data Quality
- Higher Quality Content
- 60% Fewer Hallucinations
Browse by: Latest US Patents, China's latest patents, Technical Efficacy Thesaurus, Application Domain, Technology Topic, Popular Technical Reports.
© 2025 PatSnap. All rights reserved.Legal|Privacy policy|Modern Slavery Act Transparency Statement|Sitemap|About US| Contact US: help@patsnap.com