Surgical system for cutting an anatomical structure according to at least one target plane
a surgical system and target plane technology, applied in the direction of fluid jet surgical cutters, bone drill guides, incision instruments, etc., can solve the problems of unsuitable cutting of body parts with a saw, the degree of freedom provided by the actuation unit is not suited to the plurality of cutting planes, and the planar five-bar linkage illustrated in document wo 2014
- Summary
- Abstract
- Description
- Claims
- Application Information
AI Technical Summary
Benefits of technology
Problems solved by technology
Method used
Image
Examples
Embodiment Construction
[0148]The following description is focused on knee surgery, in particular total knee arthroplasty (TKA), in which case the anatomical structure to be cut is a joint formed of the femur and the tibia.
[0149]However, the invention is not limited to this specific application, but can be applied to various applications where there is a need to perform cuts along at least one plane in a bony anatomy. In general, the invention can be used in any surgical intervention requiring at least one osteotomy step. In particular but not limited to, the invention could also be implemented in the following surgical applications: unicompartmental knee arthroplasty (UKA), tibial or femoral osteotomy, patella resurfacing, hallux valgus surgery, hip surgery for cutting the proximal femur, shoulder surgery for cutting the humeral head, spine surgery for correcting deformities and performing an osteotomy of the vertebral body, ankle surgery, maxillofacial surgery.
[0150]As will be explained in further detail...
PUM
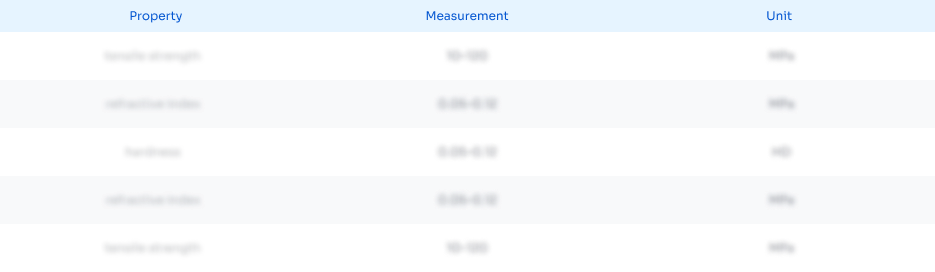
Abstract
Description
Claims
Application Information

- R&D
- Intellectual Property
- Life Sciences
- Materials
- Tech Scout
- Unparalleled Data Quality
- Higher Quality Content
- 60% Fewer Hallucinations
Browse by: Latest US Patents, China's latest patents, Technical Efficacy Thesaurus, Application Domain, Technology Topic, Popular Technical Reports.
© 2025 PatSnap. All rights reserved.Legal|Privacy policy|Modern Slavery Act Transparency Statement|Sitemap|About US| Contact US: help@patsnap.com