Semiconductor device
a technology of semiconductor devices and semiconductors, applied in semiconductor devices, semiconductor/solid-state device details, electrical apparatus, etc., can solve the problems of increasing the stiffness of the terminal, increasing the stress applied, and becoming more and more difficult to fabricate elements that meet the conditions, so as to reduce the area of each bonding portion, reduce the absolute value of thermal stress applied to each bonding portion, and suppress the peeling effect of the bonding fa
- Summary
- Abstract
- Description
- Claims
- Application Information
AI Technical Summary
Benefits of technology
Problems solved by technology
Method used
Image
Examples
first embodiment
[0048]
[0049]FIG. 1 is a plan view and a front view of a structure of a semiconductor device according to a first embodiment. FIG. 2 is a perspective view of an electrode terminal 6 and a conductive pattern 4b. In this first embodiment, like in the prerequisite art (FIG. 14), conductive patterns 4a and 4b are disposed on the insulating substrate 1, and semiconductor elements (a MOSFET chip 2 and an SBD chip 3) are bonded to the conductive pattern 4a. The electrode terminal 6 is bonded on the conductive pattern 4b.
[0050]According to the prerequisite art, ultrasonic bonding is performed at only one position on one bonding face between the electrode terminal 6 and the conductive pattern 4b. Accordingly, a recess 5 is formed by the ultrasonic bonding at one position on the upper surface of a bonding portion of the electrode terminal 6.
[0051]On the other hand, according to this first embodiment, as shown in FIG. 1, a plurality of bonding portions are provided on one bonding face 7 of the...
second embodiment
[0059]
[0060]FIG. 3 is a perspective view of an electrode terminal 6 and a conductive pattern 4b according to a second embodiment. In this second embodiment, the electrode terminal 6 is a flat plate. The root of the electrode terminal 6 is divided into two branches in the width direction. In other words, the root of the electrode terminal 6 includes two branches 6a, 6b.
[0061]As shown in FIG. 3, the branches 6a, 6b are bent to form an angle of 90° with each other in a plan view. The branch 6a is bonded to the conductive pattern 4b by ultrasonic bonding on the bonding face 7a. In the same manner, the branch 6b is bonded by the ultrasonic bonding to the conductive pattern 4b on the bonding face 7b. On the bonding faces 7a, 7b, the branches 6a, 6b are respectively bonded by the ultrasonic bonding to the conductive pattern 4b at one position. Recesses 5a, 5b are formed by the ultrasonic bonding at the upper surfaces of the branches 6a, 6b.
[0062]
[0063]In this second embodiment, the secti...
third embodiment
[0075]
[0076]FIG. 4 is a perspective view of an electrode terminal 6 and a conductive pattern 4b according to a third embodiment. In this third embodiment, the electrode terminal 6 is a flat plate. The root of the electrode terminal 6 is divided into two branches in the thickness direction. In other words, the root of the electrode terminal 6 includes two branches 6a, 6b.
[0077]As shown in FIG. 4, the branches 6a, 6b are bent in opposite directions to form an angle of 180° with each other in a plan view. The branch 6a is bonded to the conductive pattern 4b by ultrasonic bonding on the bonding face 7a. Similarly, the branch 6b is bonded by the ultrasonic bonding to the conductive pattern 4b on the bonding face 7b. Each of the branches 6a, 6b is bonded by the ultrasonic bonding to the conductive pattern 4b at one position on one of the bonding faces 7a, 7b. The total sum of the areas of the bonding faces 7a, 7b according to this third embodiment is twice as large as that of the bonding...
PUM
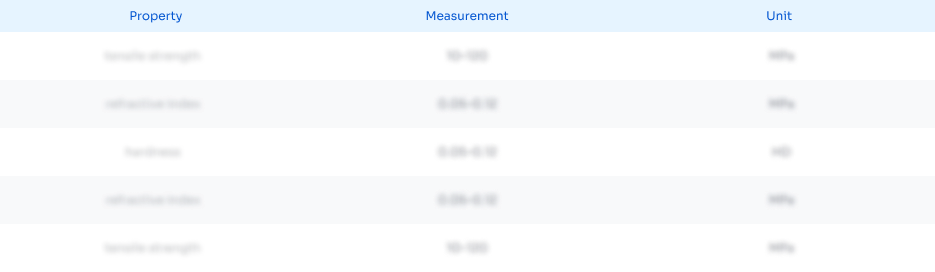
Abstract
Description
Claims
Application Information

- Generate Ideas
- Intellectual Property
- Life Sciences
- Materials
- Tech Scout
- Unparalleled Data Quality
- Higher Quality Content
- 60% Fewer Hallucinations
Browse by: Latest US Patents, China's latest patents, Technical Efficacy Thesaurus, Application Domain, Technology Topic, Popular Technical Reports.
© 2025 PatSnap. All rights reserved.Legal|Privacy policy|Modern Slavery Act Transparency Statement|Sitemap|About US| Contact US: help@patsnap.com