Electric waste gate control system sensor calibration with end-stop detection
a technology of waste gate control and sensor calibration, which is applied in the direction of electric control, instruments, machines/engines, etc., can solve the problems of waste gate valve impacting the valve seat at a high velocity, noise, vibration, and increased wear on the valve seat, etc., to achieve precise position control, faster response, and the effect of reducing the number of times
- Summary
- Abstract
- Description
- Claims
- Application Information
AI Technical Summary
Benefits of technology
Problems solved by technology
Method used
Image
Examples
Embodiment Construction
[0014]Various systems and methods are provided for detecting an end-stop position of a waste gate valve in a turbine of a turbocharger. The end-stop position of the waste gate valve may include a position where the waste gate valve suitably aligns with a valve seat to substantially prevent gas from flowing through the waste gate (e.g., less than 5% of total flow). On the other hand, the end-stop position may include a position where the waste gate valve is fully open.
[0015]In one example, an end-stop detection routine includes commanding a complete stroke of the waste gate valve from a completely open position to a completely closed position. When the waste gate valve is commanded to an end-stop position, a plurality of conditions may be checked to determine whether the waste gate valve is indeed positioned at an end-stop position. For example, the plurality of conditions may include a difference between a feedback position signal of the waste gate valve and a commanded position sig...
PUM
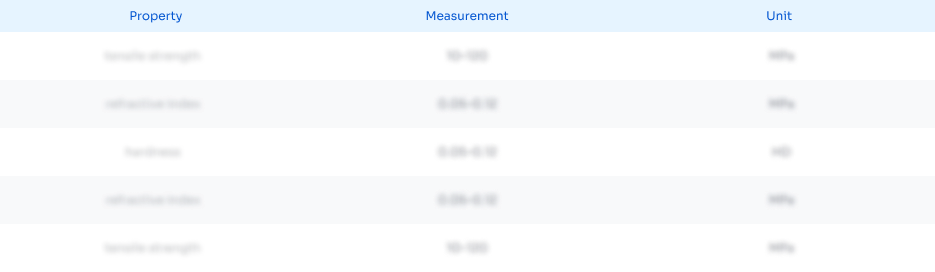
Abstract
Description
Claims
Application Information

- R&D
- Intellectual Property
- Life Sciences
- Materials
- Tech Scout
- Unparalleled Data Quality
- Higher Quality Content
- 60% Fewer Hallucinations
Browse by: Latest US Patents, China's latest patents, Technical Efficacy Thesaurus, Application Domain, Technology Topic, Popular Technical Reports.
© 2025 PatSnap. All rights reserved.Legal|Privacy policy|Modern Slavery Act Transparency Statement|Sitemap|About US| Contact US: help@patsnap.com