Method and device for controlling the temperature of steam in a boiler
a technology for controlling the temperature of steam in a boiler and steam, which is applied in the direction of flush cleaning, lighting and heating apparatus, and cleaning using liquids. it can solve the problems of changing the heat transfer and steam temperature, the boiler gradually becomes fouled, and the damage to the mechanical system. it achieves the effect of improving the steam temperature control
- Summary
- Abstract
- Description
- Claims
- Application Information
AI Technical Summary
Benefits of technology
Problems solved by technology
Method used
Image
Examples
Embodiment Construction
[0043]FIG. 1 illustrates, in highly simplified form, a steam generator. In the combustion chamber BR of the boiler K, a solid fossil fuel, for example carbon dust, is burned. The flue gas RG generated in the process is conducted through the flue gas duct RGK to the flue gas cleaning arrangement RGR. The evaporation of supplied feed water SPW takes place in the pipe systems of the evaporator chamber and of the heat exchanger. The system is conventionally constructed such that feed water is supplied from the feed water tank 1 to the feed water preheater 2 (ECO). From there, the water-steam mixture passes into the drum 3 and is supplied via the downpipes 4, the distributor collector 5 and the ascending pipes 6 to the superheater (7 or Ü) and subsequently to the turbine 8. The superheater Ü may furthermore also comprise a reheater ZÜ.
[0044]According to the invention on which this application is based, the steam temperature is controlled and regulated by virtue of a certain fouling of th...
PUM
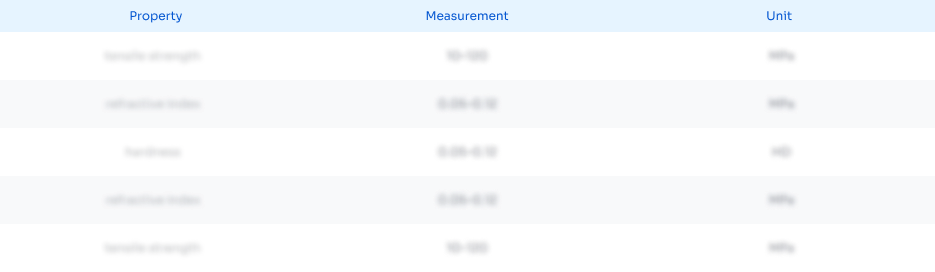
Abstract
Description
Claims
Application Information

- R&D
- Intellectual Property
- Life Sciences
- Materials
- Tech Scout
- Unparalleled Data Quality
- Higher Quality Content
- 60% Fewer Hallucinations
Browse by: Latest US Patents, China's latest patents, Technical Efficacy Thesaurus, Application Domain, Technology Topic, Popular Technical Reports.
© 2025 PatSnap. All rights reserved.Legal|Privacy policy|Modern Slavery Act Transparency Statement|Sitemap|About US| Contact US: help@patsnap.com