Cubic silicon carbide film manufacturing method, and cubic silicon carbide film-attached substrate manufacturing method
a technology of silicon carbide film and manufacturing method, which is applied in the direction of single crystal growth, polycrystalline material growth, chemistry apparatus and processes, etc., can solve the problems of limited silicon carbide (sic) substrate diameter of 3 to 4 and the difficulty of obtaining silicon carbide (sic) single crystal ingots by the pull method from a liquid phase. , to achieve the effect of fewer crystal defects and high speed
- Summary
- Abstract
- Description
- Claims
- Application Information
AI Technical Summary
Benefits of technology
Problems solved by technology
Method used
Image
Examples
example 1
[0076]FIG. 2 is a diagram representing the relationship between substrate temperature and the flow rates of carbon source gas and silicon source gas in each section of the temperature cycle of Example 1. In this example, neopentane (neo-C5H12) and dichlorosilane (SiH2Cl2) were used as carbon source gas and silicon source gas, respectively. The monocrystalline silicon epitaxial growth temperature T1 and cubic silicon carbide epitaxial growth temperature T2 were 800° C. and 1,000° C., respectively.
[0077]The carbon source gas and the silicon source gas were set to have optimum flow rates Fc1 to Fc4 and Fsi 1 to Fsi 4, respectively, for section S1 (rapid heating carbonization process), section S2 (cubic silicon carbide film epitaxial growth process), section S3 (substrate temperature lowering process), and section S4 (monocrystalline silicon epitaxial growth process).
[0078]Here, because only the carbon source gas needs to be introduced in section S1 (rapid heating carbonization process)...
example 2
[0083]FIG. 3 is a diagram representing the relationship between substrate temperature and the flow rates of carbon source gas and silicon source gas in each section of the temperature cycle of Example 2. Example 2 differs from Example 1 in that the carbon source gas flow rate Fc2=3 sccm, and that the silicon source gas flow rate Fsi 2=0 sccm.
[0084]In section S2 (cubic silicon carbide film epitaxial growth process), the carbon source gas flow rate Fc2=3 sccm, and the silicon source gas flow rate Fsi 2=0 sccm. This creates an atmosphere with the excess carbon source gas, and promotes carbonization and thus the generation of the cubic silicon carbide film.
example 3
[0085]FIG. 4 is a diagram representing the relationship between substrate temperature and the flow rates of carbon source gas and silicon source gas in each section of the temperature cycle of Example 3. Example 3 differs from Example 1 in that the carbon source gas flow rate Fc1=Fc2=5 sccm, and Fc3=Fc4=0 sccm, and that the silicon source gas flow rate Fsi 1=Fsi 2=Fsi 3=Fc4=20 sccm.
[0086]In section S1 (rapid heating carbonization process), here, both the carbon source gas and the silicon source gas are introduced. However, the introduction of the silicon source gas does not pose any problem, because the effect of carbonization by the carbon source gas far exceeds the growth by the silicon source gas.
PUM
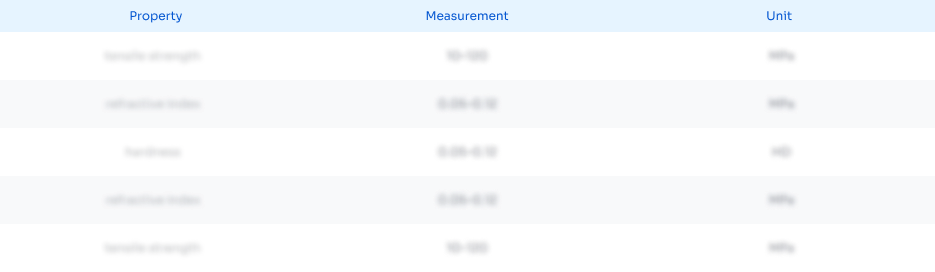
Abstract
Description
Claims
Application Information

- R&D
- Intellectual Property
- Life Sciences
- Materials
- Tech Scout
- Unparalleled Data Quality
- Higher Quality Content
- 60% Fewer Hallucinations
Browse by: Latest US Patents, China's latest patents, Technical Efficacy Thesaurus, Application Domain, Technology Topic, Popular Technical Reports.
© 2025 PatSnap. All rights reserved.Legal|Privacy policy|Modern Slavery Act Transparency Statement|Sitemap|About US| Contact US: help@patsnap.com