Air separation method and apparatus
a technology of air separation and air stream, which is applied in the direction of lighting and heating equipment, solidification, refrigeration and liquid storage, etc. it can solve the problems of increasing the energy cost of inline barrel compressors, and reducing the pressure of boosted air streams. , to achieve the effect of lessening the pressure, reducing the pressure of boosted air streams, and reducing the flow rate of such streams
- Summary
- Abstract
- Description
- Claims
- Application Information
AI Technical Summary
Benefits of technology
Problems solved by technology
Method used
Image
Examples
Embodiment Construction
[0033]With reference to FIG. 1, a cryogenic rectification plant 1 is illustrated that is designed to separate compressed and purified air and thereby to produce an oxygen product as a supercritical fluid. Cryogenic rectification plant 1 is provided with a banked heat exchanger arrangement 2 and an air separation unit 3. Air separation unit 3 preferably, for reasons that will be discussed, is provided with an argon column 62 to produce an argon product. The banked heat exchanger arrangement 2 has a lower pressure heat exchanger 22 that operates at a lower average pressure than a higher pressure heat exchanger 28 thereof. The oxygen product is discharged from the higher pressure heat exchanger 28 as an oxygen product stream 132. Additionally, a nitrogen product stream 134 is also discharged from the higher pressure heat exchanger 28. It is understood, however, that the present invention has equal application to a cryogenic rectification plant that employs only a non-banked heat exchan...
PUM
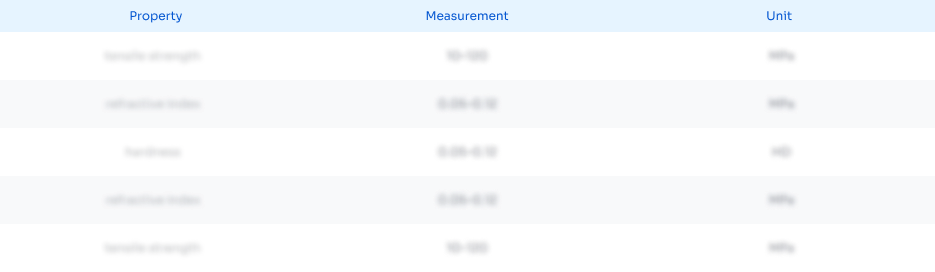
Abstract
Description
Claims
Application Information

- R&D
- Intellectual Property
- Life Sciences
- Materials
- Tech Scout
- Unparalleled Data Quality
- Higher Quality Content
- 60% Fewer Hallucinations
Browse by: Latest US Patents, China's latest patents, Technical Efficacy Thesaurus, Application Domain, Technology Topic, Popular Technical Reports.
© 2025 PatSnap. All rights reserved.Legal|Privacy policy|Modern Slavery Act Transparency Statement|Sitemap|About US| Contact US: help@patsnap.com