Swirler Vane, Swirler and Burner Assembly
a swirler and burner technology, applied in the field of swirler vanes, can solve the problems of inefficient injection of fuel, and achieve the effects of accurate control of the fuel being injected, reduced friction resistance of the injection hole and/or the injection feed hole, and improved accuracy of the injection hol
- Summary
- Abstract
- Description
- Claims
- Application Information
AI Technical Summary
Benefits of technology
Problems solved by technology
Method used
Image
Examples
Embodiment Construction
[0036]FIG. 1 shows a perspective view of a possible embodiment of an inventive swirler 2 with inventive swirler vanes 10a and a swirling zone 3 of a burner assembly having a pilot burner 1 in its centre. In this embodiment the swirler 2 is split into two parts, an inner swirler 2a and an outer swirler 2b. The swirler vanes 10a build a first part of overall swirler vanes 10, whereby the swirler vanes 10b build the second part of the overall swirler vanes 10 of the swirler 2. The inner swirler 2a comprises two or more swirler vanes 10a. Each swirler vane 10a provides fuel—preferably liquid fuel but possibly also gaseous fuel—to a swirling zone 3 of the burner assembly. In this embodiment of the swirler 2 the tip 20a of each swirler vane 10a of the inner swirler 2a is built up using laser deposition. The tip 20a as a whole can be manufactured by laser deposition or only the surface of the tip 20a is can be manufactured by laser deposition. One swirler vane 10a of the inner swirler 2a a...
PUM
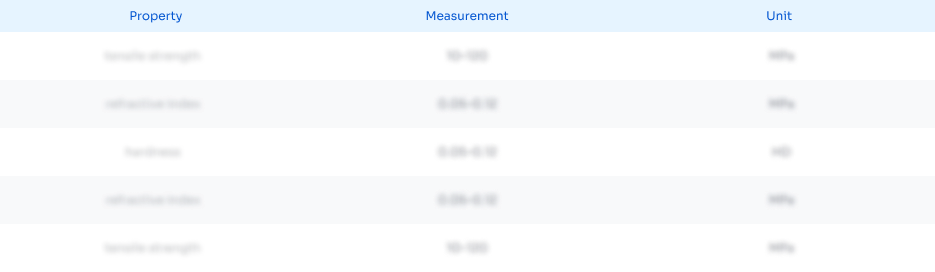
Abstract
Description
Claims
Application Information

- R&D
- Intellectual Property
- Life Sciences
- Materials
- Tech Scout
- Unparalleled Data Quality
- Higher Quality Content
- 60% Fewer Hallucinations
Browse by: Latest US Patents, China's latest patents, Technical Efficacy Thesaurus, Application Domain, Technology Topic, Popular Technical Reports.
© 2025 PatSnap. All rights reserved.Legal|Privacy policy|Modern Slavery Act Transparency Statement|Sitemap|About US| Contact US: help@patsnap.com