Exhaust gas treatment system
a gas treatment system and exhaust gas technology, applied in the direction of exhaust treatment electric control, machines/engines, mechanical equipment, etc., can solve the problems of increasing the size of the system, shortening the time it takes to start nox reduction, and increasing the entire length of the exhaust passag
- Summary
- Abstract
- Description
- Claims
- Application Information
AI Technical Summary
Benefits of technology
Problems solved by technology
Method used
Image
Examples
first embodiment
The exhaust gas treatment system 10 offers the following advantages.
(1) Since fuel, air and urea water are injected into the mixing chamber 27, the injected fuel is combusted in the mixing chamber 27 to produce flame, and the combustion gas is mixed with the injected urea water. The heat of the combustion gas accelerates the hydrolysis of urea water into ammonia in the exhaust passage 22. The mixing chamber 27 formed in the exhaust passage 22 is used not only for combustion of fuel but also for mixing of combustion gas and urea water, which allows shortening of the entire length of the exhaust passage 22 and also allows uniform mixing of combustion gas and urea water.
(2) The air injection valve 32 is located between the fuel injection valve 31 and the urea water injection valve 33 so that the urea water injection valve 33 is spaced apart from the fuel injection valve 31 and located adjacent to the air injection valve 32. This allows cooling of the urea water injection valve 33 by i...
second embodiment
wherein the fuel injection valve, the air injection valve and the urea water injection valve are integrated in the multiple valve unit 51, the number of parts of the system can be reduced, and such injection valves can be provided at a time so as to be directed toward the mixing chamber 27. Further, the air passage 53 is located between the fuel passage 52 and the urea water passage 54 so that the urea water passage 54 is spaced apart from and located radially outward of and the fuel passage 52. In this case, the injected air prevents the urea water passage 54 from receiving heat directly from the fuel passage 52, thereby preventing overheating of the urea water passage 54.
The above embodiments may be modified in various ways as exemplified below.
An oxidation catalyst may be provided downstream of the SCR catalyst 23 in the exhaust passage 22 so as to remove the excessive ammonia produced from urea water and the ammonia released from the SCR catalyst 23.
Although in the first and sec...
PUM
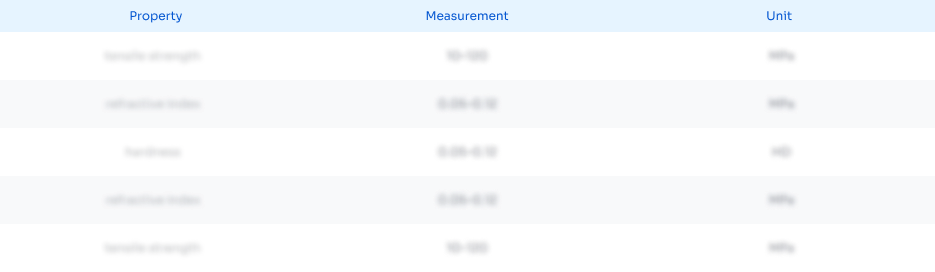
Abstract
Description
Claims
Application Information

- R&D
- Intellectual Property
- Life Sciences
- Materials
- Tech Scout
- Unparalleled Data Quality
- Higher Quality Content
- 60% Fewer Hallucinations
Browse by: Latest US Patents, China's latest patents, Technical Efficacy Thesaurus, Application Domain, Technology Topic, Popular Technical Reports.
© 2025 PatSnap. All rights reserved.Legal|Privacy policy|Modern Slavery Act Transparency Statement|Sitemap|About US| Contact US: help@patsnap.com