Process for converting biomass to coal-like material using hydrothermal carbonisation
- Summary
- Abstract
- Description
- Claims
- Application Information
AI Technical Summary
Problems solved by technology
Method used
Image
Examples
example 1
[0076]6.0 g glucose is dissolved in 24.0 g water, and citric acid is added to adjust the pH to 5. A 40 ml stainless steel autoclave is charged with the mixture and heated to 230° C. for 5 min. After cooling, the autoclave is opened, and 30 mg benzoyl peroxide is added under stirring. Then, the autoclave is sealed again, and heated to 180° C. After 90 min, the reaction is terminated by quenching. 2.9 g of hydrothermal coal containing 64 wt % carbon is obtained. The calorific value of the coal is 26 kJ / g.
example 2
[0077]200 g wood flour (sawdust) and 600 g water are formed into a slurry, and phosphoric acid is added to adjust the pH to 4. A 1 l stainless steel autoclave (manufactured by Paar, Germany), equipped with an internal thermoelement, is charged with the mixture and heated to 250° C. After exceeding the internal temperature of 240° C., the reaction is quenched after 10 min. Subsequently, 100 mg FeCl3.6 H2O and 200 mg 30% aqueous H2O2 are added at a temperature of about 100° C. The reaction mixture is heated again to 195° C., and further reacted for 3 h. After cooling and opening the autoclave, the product is separated into a solid phase (containing the hydrothermal coal) and a liquid phase. There is obtained 76 g of hydrothermal coal which contains 68 wt % carbon and can be pulverized by hand. The calorific value of the coal is 25 kJ / g.
example 3
[0078]The liquid phase separated from the reaction mixture in Example 2, while still warm (60° C.), is bubbled with air to obtain an oxidized liquid phase. Then, Example 2 is repeated except for using 200 ml of the thus-obtained oxidized liquid phase in place of the FeCl3.6 H2O and H2O2. A product is obtained which is, within the measurement accuracy, the same as that obtained in Example 2.
PUM
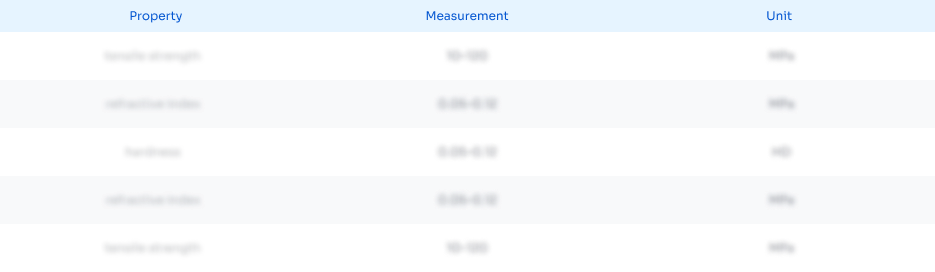
Abstract
Description
Claims
Application Information

- R&D
- Intellectual Property
- Life Sciences
- Materials
- Tech Scout
- Unparalleled Data Quality
- Higher Quality Content
- 60% Fewer Hallucinations
Browse by: Latest US Patents, China's latest patents, Technical Efficacy Thesaurus, Application Domain, Technology Topic, Popular Technical Reports.
© 2025 PatSnap. All rights reserved.Legal|Privacy policy|Modern Slavery Act Transparency Statement|Sitemap|About US| Contact US: help@patsnap.com