Program controlled dicing of a substrate using a pulsed laser beam
a laser beam and pulsed technology, applied in the direction of electrical programme control, manufacturing tools, instruments, etc., can solve the problems of inability to machine thin wafers, low yield, and use of mechanical saws, and achieve the effect of facilitating dicing and maximizing the machining ra
- Summary
- Abstract
- Description
- Claims
- Application Information
AI Technical Summary
Benefits of technology
Problems solved by technology
Method used
Image
Examples
Embodiment Construction
[0070]A laser beam may be used to dice a semiconductor wafer 10 and thereby singulate devices 11 from the wafer by scanning a Q-switched laser beam over the wafer surface using rotating mirrors in a galvanometer type system to form a pattern such as that shown in FIG. 1. Focusing of the laser beam may be achieved using a telecentric type scan lens.
[0071]In embodiments of this invention, the temporal separation of consecutive laser pulses (Δt) and the laser pulse energy (E) is varied during machining of a single or multilayered substrate in order to reduce thermal loading in different portions of the single layer or in each of the materials in the substrate and the subsequent mechanical stress or damage that results.
[0072]By way of example, a multilayered material workpiece 30 consisting of four layers 31, 32, 33 and 34 of three different material types is shown in FIG. 3(i). These materials could be, for example, a polymer material first layer 31 on a metal second layer 32 on a poly...
PUM
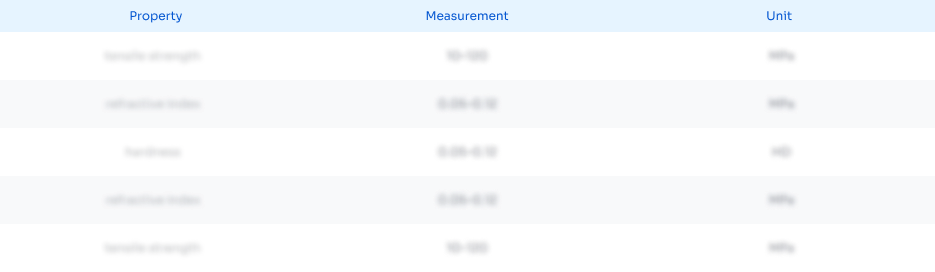
Abstract
Description
Claims
Application Information

- R&D
- Intellectual Property
- Life Sciences
- Materials
- Tech Scout
- Unparalleled Data Quality
- Higher Quality Content
- 60% Fewer Hallucinations
Browse by: Latest US Patents, China's latest patents, Technical Efficacy Thesaurus, Application Domain, Technology Topic, Popular Technical Reports.
© 2025 PatSnap. All rights reserved.Legal|Privacy policy|Modern Slavery Act Transparency Statement|Sitemap|About US| Contact US: help@patsnap.com