Device for drilling angled osteal tunnels
a technology of osteal tunnels and devices, applied in bone drill guides, medical science, surgery, etc., can solve the problems of affecting shoulder movement, affecting the normal function of ligaments, and being relatively weak, so as to weaken the bony bridge
- Summary
- Abstract
- Description
- Claims
- Application Information
AI Technical Summary
Benefits of technology
Problems solved by technology
Method used
Image
Examples
Embodiment Construction
[0060]The following detailed description of preferred embodiments is presented only for illustrative and descriptive purposes and is not intended to be exhaustive or to limit the scope and spirit of the invention. The embodiments were selected and described to best explain the principles of the invention and its practical applications. One of ordinary skill in the art will recognize that many variations can be made to the invention disclosed in this specification without departing from the scope and spirit of the invention.
[0061]Illustrative embodiments of a device and method for drilling angled osteal tunnels and anchoring sutures therein according to the present invention are shown in FIGS. 2A through 9. FIG. 2A is an elevation view of an embodiment of the present invention having a movable drill guide. FIG. 2B is a top plan view of the present invention shown in FIG. 2A, further showing the attachment of the drill guide. FIG. 2C is bottom plan view of an embodiment of the guide c...
PUM
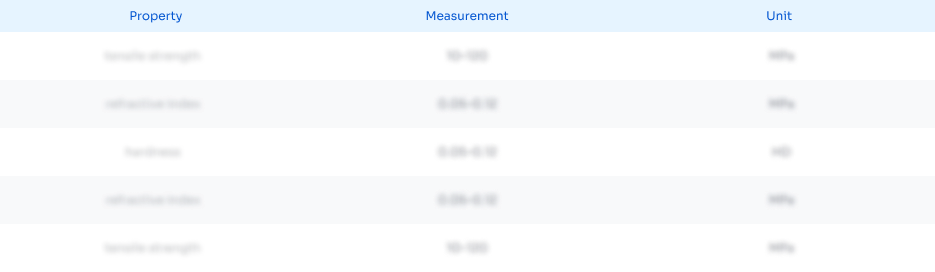
Abstract
Description
Claims
Application Information

- R&D
- Intellectual Property
- Life Sciences
- Materials
- Tech Scout
- Unparalleled Data Quality
- Higher Quality Content
- 60% Fewer Hallucinations
Browse by: Latest US Patents, China's latest patents, Technical Efficacy Thesaurus, Application Domain, Technology Topic, Popular Technical Reports.
© 2025 PatSnap. All rights reserved.Legal|Privacy policy|Modern Slavery Act Transparency Statement|Sitemap|About US| Contact US: help@patsnap.com