Light-emitting device containing a composite electroplated substrate
- Summary
- Abstract
- Description
- Claims
- Application Information
AI Technical Summary
Benefits of technology
Problems solved by technology
Method used
Image
Examples
Embodiment Construction
[0020]The first embodiment of the present application is illustrated in FIG. 1A to FIG. 1F. Referring to FIG. 1A, a growth substrate 101 is provided. A semiconductor epitaxy structure 105 is formed on the growth substrate, included at least a first conductivity type semiconductor layer 102, an active layer 103, and a second conductivity type semiconductor layer 104. In this embodiment, the first conductivity type semiconductor layer 102 is an n-GaN layer, the active layer 103 is an InGaN / GaN multiple quantum wells structure, and the second conductivity type semiconductor layer 104 is a p-GaN layer. The semiconductor epitaxy structure 105 is formed on sapphire by the epitaxy technology. The reflective layer 106 is formed on the semiconductor epitaxy structure 105 as a stack of titanium (thickness is 30 nm) / aluminum (thickness is 200 nm). It can also be as a stack of titanium / gold or titanium / silver.
[0021]Referring to FIG. 1B, a seed layer 107 is formed on the reflective layer 106 to ...
PUM
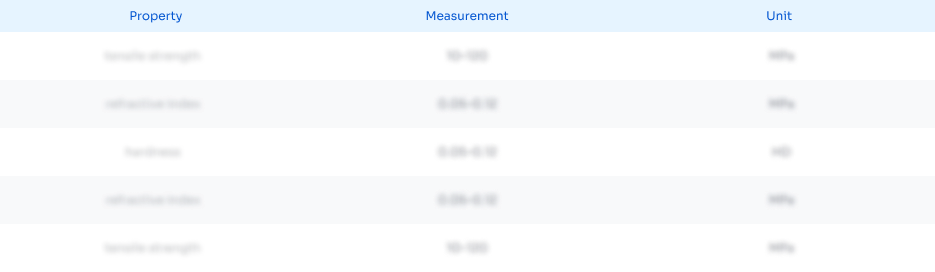
Abstract
Description
Claims
Application Information

- R&D
- Intellectual Property
- Life Sciences
- Materials
- Tech Scout
- Unparalleled Data Quality
- Higher Quality Content
- 60% Fewer Hallucinations
Browse by: Latest US Patents, China's latest patents, Technical Efficacy Thesaurus, Application Domain, Technology Topic, Popular Technical Reports.
© 2025 PatSnap. All rights reserved.Legal|Privacy policy|Modern Slavery Act Transparency Statement|Sitemap|About US| Contact US: help@patsnap.com