Compressed Coconut Coir Pith Granules and Methods for the Production and use Thereof
a technology granules, which is applied in the field of compressed coconut coir pith granules, can solve the problems of large shipping and handling costs, cumbersome use of compressed coir pith bricks for consumers, and large expansion of entire bricks with water for a relatively long tim
- Summary
- Abstract
- Description
- Claims
- Application Information
AI Technical Summary
Benefits of technology
Problems solved by technology
Method used
Image
Examples
example 1
[0041]Coir pith bricks of Sri Lankan origin were obtained from Haymark (Spring, Tex.). The bricks were out turned using a pin mill and screened through ⅜″ screen. The loose coir had a moisture content of between 10 and 17% by weight. A horticulturally acceptable surfactant was obtained from BASF, Pluronic L-62 is the name of the proprietary non-ionic surfactant. The coir was blended with 1% by weigh solution of a 1:1 mixture of surfactant and water. The surfactant treated coir was then fed into a Chilsonator Model 1.5 L×8 D Roll Compactor manufactured by Fitzpatrick Co. The roll pressure (oil pressure) was operated at between 1200 and 1800 psi. The feed screw was turning at 70 rpms. The coir left the compactor as a mixture of fines and semi-continuous ribbons. The compacts were collected and screened using a Sweco vibratory screener to +¼″. The fines were recycled back to the compactor. After about 20 lbs of compacts larger than ¼″ were collected, the material was milled in a Fitzmi...
example 2
[0042]Coir pith bricks of Sri Lankan origin were obtained from Haymark (Spring, Texas). The coir bricks were outturned using an Extructor Model RE-12 manufactured by Bepex (Minneapolis, Minn.). The coir was then milled using a Pulvicron, PC-20 (Bepex) in order to reduce the length of fibers present with the pith. The pulvicron is an air-swept mill with and internal classifier. Use of this mill is effective at reducing the fiber length and adjusting the moisture content of the coir pith by controlling the temperature and / or humidity of the air stream. Moisture content of the coir pith was typically between 10% and 15% by weight after milling. The pith was then batch blended in a ribbon blender with pulverized dolomite lime to adjust pH and 15-15-15 fertilizer (containing ammonium nitrate, ammonium sulfate, diammonium phosphate, and potassium chloride). The blended coir was compacted into ribbons using a Model MS-75 Compactor (Bepex) with a medium compression feed screw and flat (smoo...
PUM
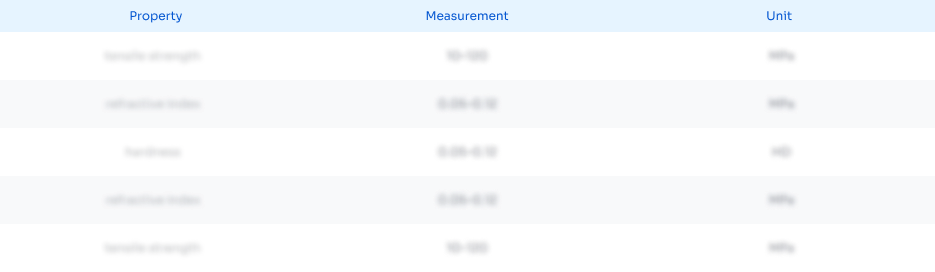
Abstract
Description
Claims
Application Information

- R&D
- Intellectual Property
- Life Sciences
- Materials
- Tech Scout
- Unparalleled Data Quality
- Higher Quality Content
- 60% Fewer Hallucinations
Browse by: Latest US Patents, China's latest patents, Technical Efficacy Thesaurus, Application Domain, Technology Topic, Popular Technical Reports.
© 2025 PatSnap. All rights reserved.Legal|Privacy policy|Modern Slavery Act Transparency Statement|Sitemap|About US| Contact US: help@patsnap.com