Lean premixed, radial inflow, multi-annular staged nozzle, can-annular, dual-fuel combustor
- Summary
- Abstract
- Description
- Claims
- Application Information
AI Technical Summary
Benefits of technology
Problems solved by technology
Method used
Image
Examples
Embodiment Construction
[0039]The following embodiments of the present invention have many advantages, including several innovative and unique features: (1) allowing for multiple (e.g., six) premixing nozzles (per can) and a combustor-chamber cap to be replaced with just one large radial nozzle and a liner modification, thereby achieving a significant part-count reduction, a cost savings, and a dramatic simplification of the combustor's head-end; (2) using a dome-diffuser design to backside, convectively cool the liner's dome, while, simultaneously recovering static pressure prior to premixing the fuel and air in the large radial nozzle, thereby causing less parasitic pressure loss and malting more air available for premixing; (3) providing the capacity to rapidly (e.g. <3 msec) and thoroughly vaporize and mix large quantities of fuel (˜2 lbm / sec) and air (˜60 lbm / sec) at a relatively low pressure drop (e.g., <4%); and (4) using either gas fuel or liquid fuel, it is more robust dynamically and less prone t...
PUM
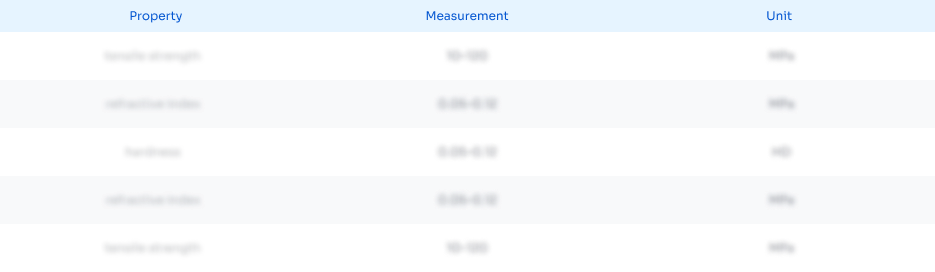
Abstract
Description
Claims
Application Information

- R&D
- Intellectual Property
- Life Sciences
- Materials
- Tech Scout
- Unparalleled Data Quality
- Higher Quality Content
- 60% Fewer Hallucinations
Browse by: Latest US Patents, China's latest patents, Technical Efficacy Thesaurus, Application Domain, Technology Topic, Popular Technical Reports.
© 2025 PatSnap. All rights reserved.Legal|Privacy policy|Modern Slavery Act Transparency Statement|Sitemap|About US| Contact US: help@patsnap.com