Ground Anchor
a ground anchor and lateral load technology, applied in the direction of bulkheads/piles, building types, building constructions, etc., can solve the problems of limited ground anchors that cannot resist lateral loads, in-situ stabilisation is time-consuming, labour-intensive, etc., to achieve effective compression of soil in a given zone, increase the effective diameter of screw flight, and improve the ground holding ability
- Summary
- Abstract
- Description
- Claims
- Application Information
AI Technical Summary
Benefits of technology
Problems solved by technology
Method used
Image
Examples
first embodiment
[0079]Referring to FIGS. 1 to 6, there is shown a ground anchor 10 according to a The ground anchor 10 comprises an anchor shaft 11 and an anchoring screw 13 fitted onto the anchoring shaft adjacent the lower end thereof. The anchoring shaft 11 is of polygonal cross-sectional, and in the arrangement shown is of rectangular cross-section with four side walls 12. The anchoring shaft 11 is configured at its bottom end 15 for ground penetration. In the arrangement shown, the bottom end is provided with a point 17 generated by an angular cut on the shaft. The point 17 serves to penetrate the ground and also displace soil sidewardly as it advances through the ground.
[0080]The upper end 19 of the anchor shaft 11 is configured to receive torque applied thereto. The upper end 19 may be configured to receive a tool such as a torque tube through which torque may be applied to the anchor shaft 11. The torque may be applied manually or through a power device, such as for example, a portable ele...
third embodiment
[0095]Referring now to FIG. 8, there is shown an anchoring screw 60 for a ground anchor according to a In this embodiment, the leading edge 27 of the spiral flight 23 is not generally straight (as was the case with the previous embodiments) but rather it is configured to present a curved profile 61 towards the radially outer end thereof. The curved profile 61 comprises a curve which merges with the outer circumference 33. The curved configuration serves to displace rock and debris in the path of the leading edge 27 outwardly away from the rotating helix as it winds into the ground.
fourth embodiment
[0096]With the arrangement shown in FIG. 8, the curved profile 61 can increase the horizontal component of separation between the leading and trailing edges of the screw. In certain circumstances, such separation may be undesirable as it may disrupt the uniformity of loading on the anchoring screw. With a view to addressing this deficiency, the anchoring screw may be configured so that there is some vertical overlap between the leading and trailing edges. Such an arrangement is provided by the next embodiment. Referring now to FIG. 9, there is shown an anchoring screw 70 for a ground anchor according to a In this embodiment, the leading edge 27 incorporates the rounded profile 61 of the previous embodiment but the relative positions of the leading and trailing edges are moved angularly such that there is overlap therebetween.
PUM
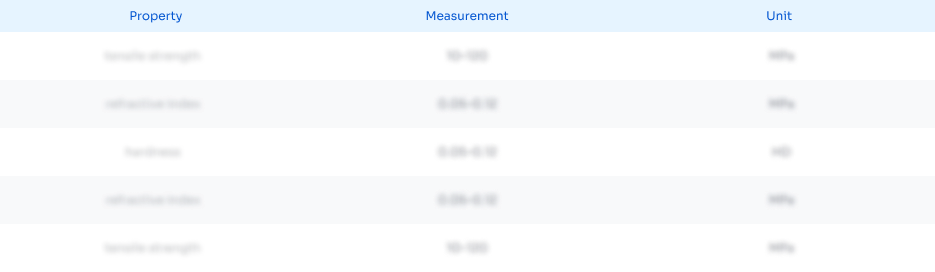
Abstract
Description
Claims
Application Information

- R&D
- Intellectual Property
- Life Sciences
- Materials
- Tech Scout
- Unparalleled Data Quality
- Higher Quality Content
- 60% Fewer Hallucinations
Browse by: Latest US Patents, China's latest patents, Technical Efficacy Thesaurus, Application Domain, Technology Topic, Popular Technical Reports.
© 2025 PatSnap. All rights reserved.Legal|Privacy policy|Modern Slavery Act Transparency Statement|Sitemap|About US| Contact US: help@patsnap.com