Impeller with Anti-vapor lock mechanism
- Summary
- Abstract
- Description
- Claims
- Application Information
AI Technical Summary
Benefits of technology
Problems solved by technology
Method used
Image
Examples
Embodiment Construction
[0057]The present invention is directed to a pump for pumping water, sewage, or other liquid material from one location to another. The pump includes an impeller, or impeller that is rotated in moderately close proximity to a stationary plate or stator. The stationary plate has a central, coaxial inlet through which liquid passes, and is thereafter conveyed by centrifugal force along the impeller-plate spacing to an outlet at the periphery of the impeller and the plate.
[0058]The pump may be any conventionally available pump such as centrifugal pump, an impeller pump, or a mixed flow. Preferably, the pump is a centrifugal pump, such as a centrifugal rotary bilge pump that is well known in the art.
[0059]Centrifugal pumps are classified into three categories—submersible, dewatering and trash.
[0060]Submersible pumps offer contractors versatility on the job site. These pumps are, by definition, submersible in water containing solids up to one-quarter inch in diameter and less than 10 per...
PUM
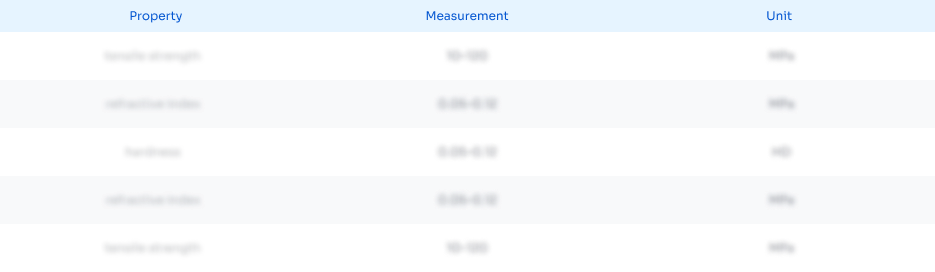
Abstract
Description
Claims
Application Information

- R&D
- Intellectual Property
- Life Sciences
- Materials
- Tech Scout
- Unparalleled Data Quality
- Higher Quality Content
- 60% Fewer Hallucinations
Browse by: Latest US Patents, China's latest patents, Technical Efficacy Thesaurus, Application Domain, Technology Topic, Popular Technical Reports.
© 2025 PatSnap. All rights reserved.Legal|Privacy policy|Modern Slavery Act Transparency Statement|Sitemap|About US| Contact US: help@patsnap.com