Cut-Resistant Glove
- Summary
- Abstract
- Description
- Claims
- Application Information
AI Technical Summary
Benefits of technology
Problems solved by technology
Method used
Image
Examples
example 1
[0080]One stainless thin wire with a thickness of 25 μm (SUS 304 stainless steel wire, manufactured by Nippon Seisen Co., Ltd.) and one ultra high molecular weight polyethylene filament yarn with 400D / 390F (trade name: Dyneema SK 60, manufactured by Toyobo Co., Ltd.) were united together by gently winding the ultra high molecular weight polyethylene filament yarn around the stainless thin wire at 33 turns / m and used as a core and one wooly-processed nylon fiber with 70D / 24F (a nylon yarn, manufactured by Hantex Co., Ltd.) was wrapped at 634 turns / m around the core and further one wooly-processed nylon fiber with 70D / 24F (a nylon yarn, manufactured by Hantex Co., Ltd.) was wrapped at 634 turns / m thereon in the opposite direction to form a covering layer and a composite yarn was obtained.
[0081]Next, using the obtained composite yarn, a glove was knitted by a 10G knitting machine. The knitted glove was fitted on a glove mold and immersed in the coagulant, then immersed in the nitrile b...
example 2
[0083]One stainless thin wire with a thickness of 25 μm (SUS 304 stainless steel wire, manufactured by Nippon Seisen Co., Ltd.) and one ultra high molecular weight polyethylene filament yarn with 400D / 390F (trade name: Dyneema SK60, manufactured by Toyobo Co., Ltd.) were united together by gently winding the ultra high molecular weight polyethylene filament yarn around the stainless thin wire at 10 turns / m and used as a core and one wooly-processed nylon fiber with 70D / 24F (a nylon yarn, manufactured by Hantex Co., Ltd.) was wrapped at 634 turns / m around the core and further one wooly-processed nylon fiber with 70D / 24F (a nylon yarn, manufactured by Hantex Co., Ltd.) was wrapped at 634 turns / m thereon in the opposite direction to form a covering layer and a composite yarn was obtained.
[0084]Next, using the obtained composite yarn, a glove was knitted by a 10G knitting machine. The knitted glove was fitted on a glove mold and immersed in the coagulant, then immersed in the nitrile bu...
example 3
[0086]One stainless thin wire with a thickness of 25 μm (SUS 304 stainless steel wire, manufactured by Nippon Seisen Co., Ltd.) and one ultra high molecular weight polyethylene filament yarn with 400D / 390F (trade name: Dyneema SK60, manufactured by Toyobo Co., Ltd.) were united together by gently winding the ultra high molecular weight polyethylene filament yarn around the stainless thin wire at 55 turns / m and used as a core and one wooly-processed nylon fiber with 70D / 24F (a nylon yarn, manufactured by Hantex Co., Ltd.) was wrapped at 634 turns / m around the core and further one wooly-processed nylon fiber with 70D / 24F (a nylon yarn, manufactured by Hantex Co., Ltd.) was wrapped at 634 turns / m thereon in the opposite direction to form a covering layer and a composite yarn was obtained.
[0087]Next, using the obtained composite yarn, a glove was knitted by a 10G knitting machine. The knitted glove was fitted on a glove mold and immersed in the coagulant, then immersed in the nitrile bu...
PUM
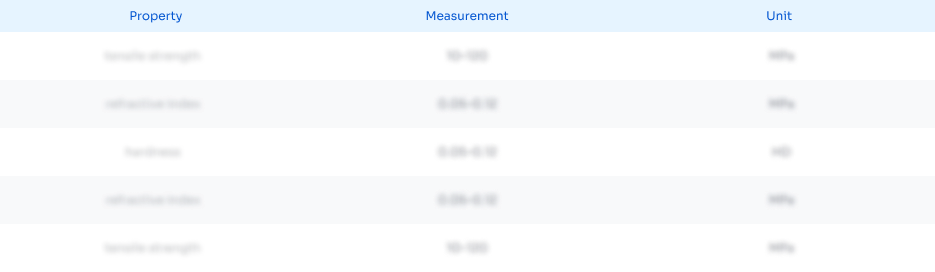
Abstract
Description
Claims
Application Information

- R&D Engineer
- R&D Manager
- IP Professional
- Industry Leading Data Capabilities
- Powerful AI technology
- Patent DNA Extraction
Browse by: Latest US Patents, China's latest patents, Technical Efficacy Thesaurus, Application Domain, Technology Topic, Popular Technical Reports.
© 2024 PatSnap. All rights reserved.Legal|Privacy policy|Modern Slavery Act Transparency Statement|Sitemap|About US| Contact US: help@patsnap.com