Atomic force microscope technique for minimal tip damage
a technology of atomic force microscope and afm, which is applied in the direction of mechanical measurement arrangement, mechanical roughness/irregularity measurement, instruments, etc., can solve the problems of afm tip damage, loss of accuracy and precision, and abrupt and sharp phase signal reversal
- Summary
- Abstract
- Description
- Claims
- Application Information
AI Technical Summary
Benefits of technology
Problems solved by technology
Method used
Image
Examples
Embodiment Construction
[0023]The present invention provides a means to determine and use a critical feedback setpoint with an atomic force microscope (AFM) in an effort to avoid tip damage and remain in non-contact attractive mode during use.
An Exemplary AFM System
[0024]FIG. 1 is a simplified functional block diagram of an atomic force microscope 100 for dynamic mode operation including a probe / sample positioning apparatus and a feedback system using an amplitude feedback setpoint 140 in accordance with one embodiment of the present invention. A phase feedback setpoint (not shown) may be employed in other embodiments of the invention, although this description will focus primarily on an amplitude feedback setpoint 140 to maintain consistency and avoid confusion.
[0025]A probe tip 102 on the end of a cantilever 104 may be oscillated at a known free oscillation amplitude and frequency near the cantilever resonant frequency by a tip oscillator 106. The cantilever resonant frequency may be around 300 kHz, and ...
PUM
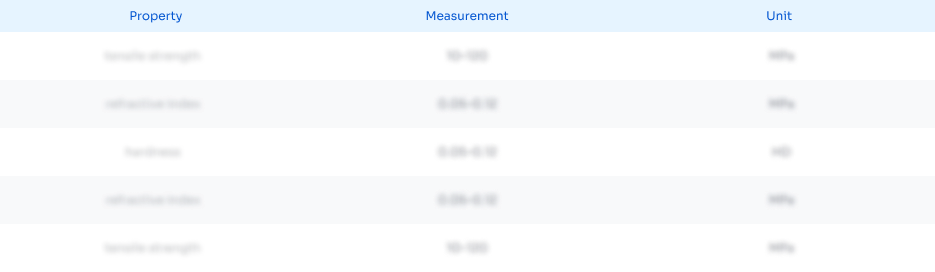
Abstract
Description
Claims
Application Information

- R&D
- Intellectual Property
- Life Sciences
- Materials
- Tech Scout
- Unparalleled Data Quality
- Higher Quality Content
- 60% Fewer Hallucinations
Browse by: Latest US Patents, China's latest patents, Technical Efficacy Thesaurus, Application Domain, Technology Topic, Popular Technical Reports.
© 2025 PatSnap. All rights reserved.Legal|Privacy policy|Modern Slavery Act Transparency Statement|Sitemap|About US| Contact US: help@patsnap.com