Finned helicoidal heat exchanger
a heat exchanger and helical coil technology, applied in the field of heat exchangers, can solve the problems of reducing the overall heat exchange capability of the coil, limiting the types of fin materials that can be used, and excessive pressure drop in the first fluid, so as to enhance the exchange of thermal energy.
- Summary
- Abstract
- Description
- Claims
- Application Information
AI Technical Summary
Benefits of technology
Problems solved by technology
Method used
Image
Examples
Embodiment Construction
[0025] The following description of the preferred embodiment(s) is merely exemplary in nature and is in no way intended to limit the invention, its application, or uses.
[0026] The embodiments disclosed below are not intended to be exhaustive or limit the invention to the precise forms disclosed below. Rather, the embodiments are chosen and described so that others skilled in the art may utilize their teachings.
[0027] Referring to the accompanying drawings in which like reference numbers indicate like elements, FIGS 1a-1c illustrate a finned helicoidal heat exchanger 20. The helicoidal heat exchanger 20 includes a heat transfer tube 22 arranged substantially in the shape of a continuous helicoidal tube. The helicoidal heat exchanger 20 also includes a fin 21 secured to the external surfaces of the heat transfer tube 22. FIGS 1a-1c illustrate an embodiment having a plurality of evenly spaced fins 21A, 21B secured to the external surfaces of the heat transfer tube 22 and extending ou...
PUM
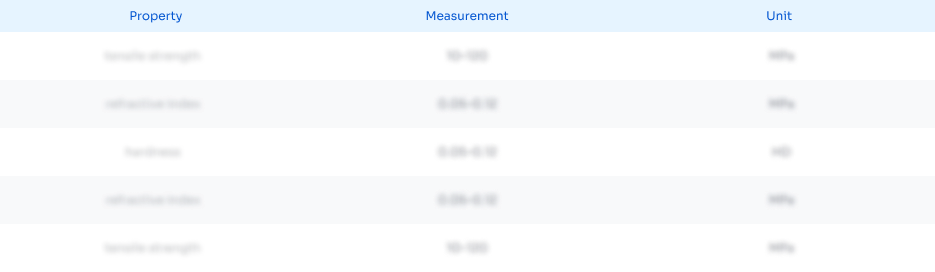
Abstract
Description
Claims
Application Information

- R&D
- Intellectual Property
- Life Sciences
- Materials
- Tech Scout
- Unparalleled Data Quality
- Higher Quality Content
- 60% Fewer Hallucinations
Browse by: Latest US Patents, China's latest patents, Technical Efficacy Thesaurus, Application Domain, Technology Topic, Popular Technical Reports.
© 2025 PatSnap. All rights reserved.Legal|Privacy policy|Modern Slavery Act Transparency Statement|Sitemap|About US| Contact US: help@patsnap.com