Cryostat configuration with cryocooler and gas gap heat transfer device
a cryostat and heat transfer device technology, applied in the field of cryostat configuration, can solve the problem of not being able to completely prevent the vibration of the cryostat cold head, and achieve the effects of reducing the number of refilling processes, reducing the loss of helium, and reducing the number of helium loss
- Summary
- Abstract
- Description
- Claims
- Application Information
AI Technical Summary
Benefits of technology
Problems solved by technology
Method used
Image
Examples
Embodiment Construction
[0027]FIG. 1 shows an embodiment of the inventive cryostat configuration with an outer jacket 1 and a helium container 2 disposed therein. The helium container is connected to the outer jacket 1 via suspension tubes 3. A two-stage cold head 7 of a cryocooler is installed in a neck tube 4 whose upper warm end 5 is connected to the outer jacket 1 and whose lower cold end 6 is connected to the helium container 2. The helium container 2 is surrounded by a radiation shield 8 which is connected in a heat-conducting manner to the suspension tubes 3 and also to a contact surface 9 on the neck tube 4 of the helium container 2. The cold head 7 is slightly lifted to produce a gas gap 13 between a cold surface 10 on the first cold stage 11 of the cold head 7 and the neck tube 4 contact surface 9 which is connected in a heat-conducting manner to the radiation shield 8 via a fixed thermal bridge 12. Heat is transferred from the radiation shield 8 to the cold stage 11 of the cold head 7 via the na...
PUM
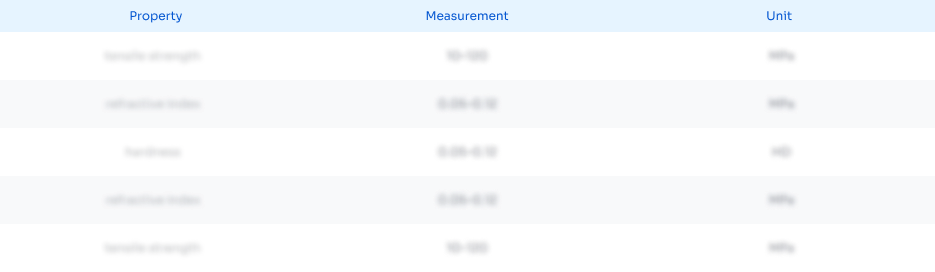
Abstract
Description
Claims
Application Information

- R&D
- Intellectual Property
- Life Sciences
- Materials
- Tech Scout
- Unparalleled Data Quality
- Higher Quality Content
- 60% Fewer Hallucinations
Browse by: Latest US Patents, China's latest patents, Technical Efficacy Thesaurus, Application Domain, Technology Topic, Popular Technical Reports.
© 2025 PatSnap. All rights reserved.Legal|Privacy policy|Modern Slavery Act Transparency Statement|Sitemap|About US| Contact US: help@patsnap.com