Pre-processing assembly for pre-processing fuel feedstocks for use in a fuel cell system
- Summary
- Abstract
- Description
- Claims
- Application Information
AI Technical Summary
Benefits of technology
Problems solved by technology
Method used
Image
Examples
example 1
[0048] The pre-processing assembly 108 has been optimized for processing fuel feedstock comprising oxygen and methane for use in a 300 kW Direct Fuel Cell power plant. The deoxidizer bed 204 comprises a G-74D catalyst and has a volume of 0.7 cubic feet. The pre-reforming bed 206 comprises a C11-PR catalyst and has a volume of 2.5 cubic feet. The deoxidizer bed 204 is approximately 4 inches in thickness and the pre-reforming bed 206 is approximately 14.5 inches in thickness. The common vessel 202 is made from 304 / 310 stainless steel and has a volume of 4 cubic feet and a diameter of 20 inches.
[0049] The optimal temperatures of the fuel feedstock entering the vessel 202 through the inlet 208 and of the pre-processed fuel feedstock exiting the vessel 202 through the outlet 210 are approximately 300 to 490° C. The optimal operating temperature range of the deoxidizer bed 204 is between 300° C. and 600° C., and the optimal operating temperature range of the pre-reforming bed 206 is betw...
example 2
[0051] In this example, the pre-processing assembly 108 of Example 1 has also been optimized for processing hydrocarbon fuels contaminated with up to 10% oxygen. The optimal temperature range of the fuel feedstock entering the vessel 202 through inlet 208 is approximately 310° C. to 500° C.
[0052] The deoxidizing function of the pre-processing assembly 108 of FIG. 2 has been demonstrated with fuels containing oxygen such as anaerobic digester gas, coal mine methane, and peak shave gas. The deoxidizing performance of the assembly 108 of this example was tested at varied inlet temperatures of the fuel feedstock entering the assembly 108, and varied oxygen contents of the hydrocarbon fuels. FIG. 3 shows tabulated data of deoxidizer performance summarizing the results of these tests. In the testing procedure, the oxygen content of the inlet fuel feedstock was measured, and the fuel feedstock was pre-heated to various temperatures ranging from 312° C. to 439° C. before entering the assem...
example 3
[0060] The pre-processing assembly of FIG. 4 has been optimized for processing fuel comprising propane and up to 5% propylene for use in a 300 kW Direct Fuel Cell power plant. The deoxidizer bed 204 comprises a G-74D catalyst and has a volume of 0.7 cubic feet. The propane processor bed 301 comprises an FCR-HC59 anti-carbon catalyst manufactured by Sud Chemie and has a volume of 0.75 cubic feet, and the pre-reforming bed 206 comprises a C11-PR catalyst and has a volume of 1.7 cubic feet. The vessel 202 is made from 304 / 310 stainless steel and has a volume of 4 cubic feet.
[0061] The optimal temperature of the fuel feedstock entering the vessel 202 through the inlet 208 is approximately 350° C. and the temperature of the pre-processed fuel exiting the vessel 202 through the outlet 210 is approximately 350° C. The deoxidizer bed 204 is adapted to operate at a temperature between 300° and 600° C., while the propane processor bed 301 and the pre-reforming bed 206 are adapted to operate ...
PUM
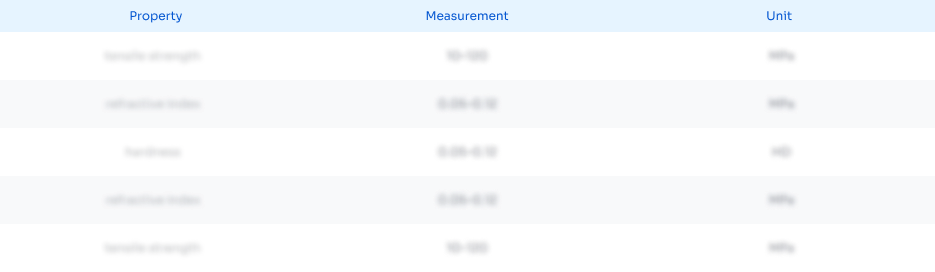
Abstract
Description
Claims
Application Information

- R&D
- Intellectual Property
- Life Sciences
- Materials
- Tech Scout
- Unparalleled Data Quality
- Higher Quality Content
- 60% Fewer Hallucinations
Browse by: Latest US Patents, China's latest patents, Technical Efficacy Thesaurus, Application Domain, Technology Topic, Popular Technical Reports.
© 2025 PatSnap. All rights reserved.Legal|Privacy policy|Modern Slavery Act Transparency Statement|Sitemap|About US| Contact US: help@patsnap.com