System and method for high-performance scanner calibration
a scanning system and high-performance technology, applied in the field of scanning system calibration, can solve the problems of noticeably speeding up scan and copy time, and achieve the effects of reducing the memory requirement for offset and gain calibration, reducing the size/performance bottleneck of the scanner system, and increasing performan
- Summary
- Abstract
- Description
- Claims
- Application Information
AI Technical Summary
Benefits of technology
Problems solved by technology
Method used
Image
Examples
Embodiment Construction
[0021]FIG. 1 shows a basic block diagram for an optical reduction scanner (which is often incorrectly labeled a CCD scanner). Charge coupled device (CCD) elements refer to the technology of the image sensor, in one embodiment. CCD image sensors have historically been used with optical reduction scanners, hence the confusion. The following is an explanation of the basic operation of this type of scanner. Of course, it will be readily understood that the present invention may be used with a wide variety of scanners.
[0022] A white light source 101 such as a fluorescent bulb is used to illuminate a line of the target image 102. This type of light source contains the red, green, and blue wavelengths of light. The light reflects off of the target image and is directed through a series of optical elements 103 that shrink the image down to the size of the small image sensor 104.
[0023] The image sensor 104 typically contains three rows of elements. As shown in FIG. 2, each row (201, 202 an...
PUM
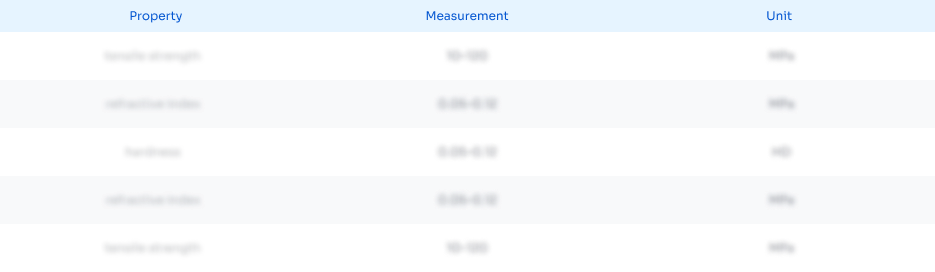
Abstract
Description
Claims
Application Information

- R&D
- Intellectual Property
- Life Sciences
- Materials
- Tech Scout
- Unparalleled Data Quality
- Higher Quality Content
- 60% Fewer Hallucinations
Browse by: Latest US Patents, China's latest patents, Technical Efficacy Thesaurus, Application Domain, Technology Topic, Popular Technical Reports.
© 2025 PatSnap. All rights reserved.Legal|Privacy policy|Modern Slavery Act Transparency Statement|Sitemap|About US| Contact US: help@patsnap.com