Monitoring of flames using optical fibers and video camera vision system
a technology of optical fibers and video cameras, applied in the direction of combustion control, fuel supply regulation, combustion regulation, etc., can solve the problems of large limitation, failure to use, and failure to meet the needs of the user
- Summary
- Abstract
- Description
- Claims
- Application Information
AI Technical Summary
Benefits of technology
Problems solved by technology
Method used
Image
Examples
Embodiment Construction
[0039] The light-receiving end of the optical fiber is located at an ideal place in or on the burner housing to view the flame; the tip of the fiber is usually inside a cool air stream. Dust will not collect on the sensing head since there is a constant flow of air across it. The fiber could be made of glass or silicon quartz material, which can withstand high temperatures normally encountered in the furnace. Stainless steel tube sheathing protects the fiber on the sides. Such optical fiber cables are commercially available.
[0040] The flame detection system has several self-checking features. [0041] 1. The fiber bundle inside the cable can have one or more individual fibers. They display individual glows at the other end. When two fibers are used, it will display two distinct dots of glows within the circle at the other end. If one fiber should develop a defect, for example due to a break in the fiber due to long usage, the other fiber will be proving that the flame is on. [0042] 2...
PUM
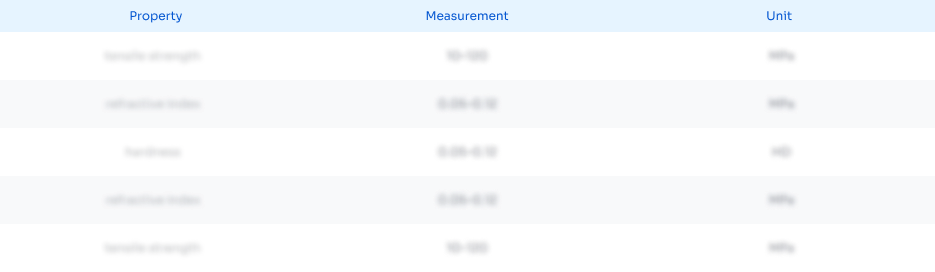
Abstract
Description
Claims
Application Information

- R&D
- Intellectual Property
- Life Sciences
- Materials
- Tech Scout
- Unparalleled Data Quality
- Higher Quality Content
- 60% Fewer Hallucinations
Browse by: Latest US Patents, China's latest patents, Technical Efficacy Thesaurus, Application Domain, Technology Topic, Popular Technical Reports.
© 2025 PatSnap. All rights reserved.Legal|Privacy policy|Modern Slavery Act Transparency Statement|Sitemap|About US| Contact US: help@patsnap.com