High frequency dynamics resonator assembly
a high frequency dynamic and resonator technology, applied in the field of resonators, can solve the problems of affecting the performance of the combustor, exposing the resonator to a heavily non-uniform flow and pressure environment, and destroying the hardware of the combustor quickly
- Summary
- Abstract
- Description
- Claims
- Application Information
AI Technical Summary
Benefits of technology
Problems solved by technology
Method used
Image
Examples
Embodiment Construction
[0030] Aspects of the present invention address the shortcomings of prior resonator designs, particularly when such resonators are placed in non-uniform flow and pressure environments. Aspects of the present invention relate to resonators including one or more features for delivering a more predictable pressure field to the resonator and / or for more evenly distributing the pressure prior to impinging on the resonator. Such features can include a flow scoop or another box volume. Aspects of the present invention can help to bring the actual conditions experienced by the resonator more in line with assumed design considerations.
[0031] Embodiments of the invention will be explained in the context of a resonator for a turbine engine. Embodiments of the invention are shown in FIGS. 6-8, but the present invention is not limited to the illustrated structure or application. For example, the resonator configurations according to the present invention can be used an any section of the engine...
PUM
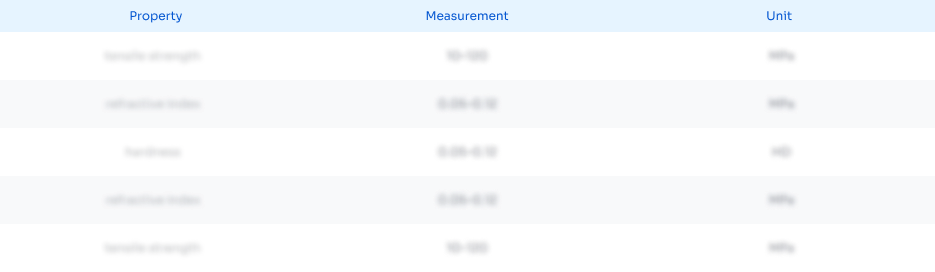
Abstract
Description
Claims
Application Information

- R&D
- Intellectual Property
- Life Sciences
- Materials
- Tech Scout
- Unparalleled Data Quality
- Higher Quality Content
- 60% Fewer Hallucinations
Browse by: Latest US Patents, China's latest patents, Technical Efficacy Thesaurus, Application Domain, Technology Topic, Popular Technical Reports.
© 2025 PatSnap. All rights reserved.Legal|Privacy policy|Modern Slavery Act Transparency Statement|Sitemap|About US| Contact US: help@patsnap.com