[method of fabricating polysilicon film]
a technology of polysilicon film and polysilicon array, which is applied in the direction of basic electric elements, electrical equipment, semiconductor devices, etc., can solve the problems of foregoing process problems, and achieve the effect of increasing output and effective improvemen
- Summary
- Abstract
- Description
- Claims
- Application Information
AI Technical Summary
Benefits of technology
Problems solved by technology
Method used
Image
Examples
first embodiment
[0026] Referring to FIGS. 2A to 2E, show the cross sectional views illustrating the progression of the process of a method of fabricating a polysilicon (poly-Si) thin film according to the first embodiment of the present invention.
[0027] Referring to FIG. 2A, a substrate 200 is provided, wherein the material of the substrate 200 includes a silicon wafer, a glass substrate or a plastic substrate, for example. An insulating layer 202 is formed over the substrate 200, wherein the insulating layer 202 includes silicon dioxide can be formed by performing a conventional deposition process such as Low Pressure Chemical Vapor Deposition (LPVCD), Plasma Enhanced Chemical Vapor Deposition (PECVD) or sputtering. Thereafter a first a-Si layer 204, which can be formed by performing a conventional process such as LPVCD, PECVD or sputtering, is formed over the insulating layer 202. Further, a cap layer 206 is formed over the first a-Si layer 204, wherein the material of the cap layer 206 includes...
second embodiment
[0033] Referring to the FIGS. 3A to 3F, show the cross sectional views illustrating the progression of the process of a method of fabricating a poly-Si film according to a second embodiment of the present invention.
[0034] Referring to FIG. 3A, a substrate 300 is provided, wherein the material of the substrate 300 includes, for example, a silicon wafer, a glass or a plastic. An insulating layer 302 is formed over the substrate 300, wherein the material of the insulating layer 302 includes, for example, a silicon dioxide, and the insulating layer 302 can be formed by, for example, performing a conventional deposition process such as a LPVCD, a PECVD or a sputtering. Thereafter, a first a-Si layer 304 is formed over the insulating layer 302, by performing, for example, a LPCVD, PECVD or sputtering process.
[0035] Further, a cap layer 306 is formed over the first a-Si layer 304, wherein the material of the cap layer 306 includes temptemp, for example, silicon dioxide, and the cap layer...
PUM
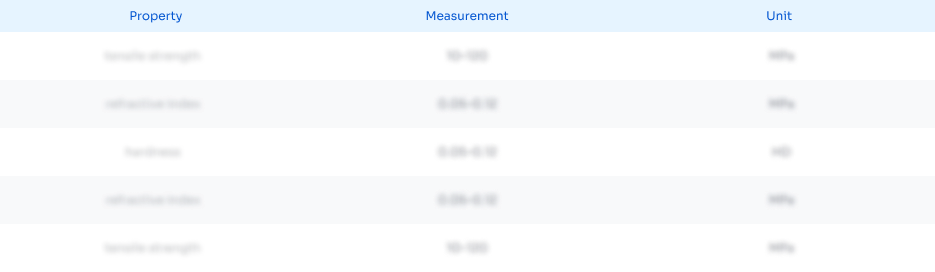
Abstract
Description
Claims
Application Information

- R&D
- Intellectual Property
- Life Sciences
- Materials
- Tech Scout
- Unparalleled Data Quality
- Higher Quality Content
- 60% Fewer Hallucinations
Browse by: Latest US Patents, China's latest patents, Technical Efficacy Thesaurus, Application Domain, Technology Topic, Popular Technical Reports.
© 2025 PatSnap. All rights reserved.Legal|Privacy policy|Modern Slavery Act Transparency Statement|Sitemap|About US| Contact US: help@patsnap.com