High-speed diaphragm valve for atomic layer deposition
a diaphragm valve, high-speed technology, applied in the direction of diaphragm valves, engine diaphragms, water supply installations, etc., can solve the problems of slow valve speed increase, compress or expand gas trapped in enclosed space, etc., to reduce the efficiency of ald reactor, reduce the amount of time, and slow the movement of the diaphragm
- Summary
- Abstract
- Description
- Claims
- Application Information
AI Technical Summary
Benefits of technology
Problems solved by technology
Method used
Image
Examples
Embodiment Construction
[0020]FIG. 1 is an isometric section view of a precursor material delivery system 100 of an ALD reactor 102, which comprises an exemplary environment of use for valves 104a-104e, in accordance with a first preferred embodiment. With reference to FIG. 1, a supply of precursor material is stored in a precursor container 106, where it is heated and vaporized before flowing through a flow path 110 of the precursor material delivery system 100 (generally from left to right in FIG. 1) and into a reaction chamber 112. ALD reactor 102 will typically have two or more precursor material delivery systems 100 connected to reaction chamber 112. Precursor material delivery system 100 includes electric heaters 116 and 118 for heating precursor materials in the flow path 110. Valves 104a-104e are used to control the flow of precursor material and regulate pressure of the precursor vapor at different stages in precursor material delivery system 100.
[0021] Precursor material delivery system 100 pref...
PUM
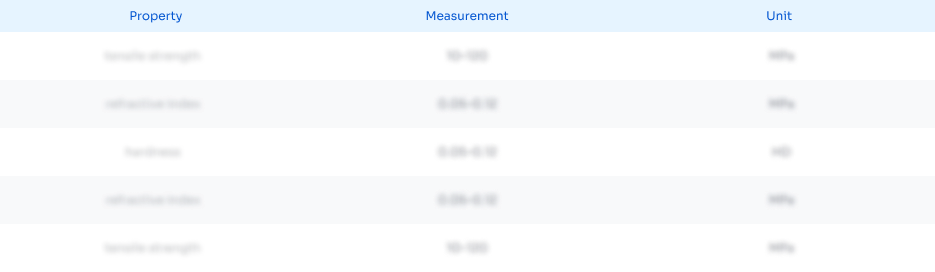
Abstract
Description
Claims
Application Information

- R&D
- Intellectual Property
- Life Sciences
- Materials
- Tech Scout
- Unparalleled Data Quality
- Higher Quality Content
- 60% Fewer Hallucinations
Browse by: Latest US Patents, China's latest patents, Technical Efficacy Thesaurus, Application Domain, Technology Topic, Popular Technical Reports.
© 2025 PatSnap. All rights reserved.Legal|Privacy policy|Modern Slavery Act Transparency Statement|Sitemap|About US| Contact US: help@patsnap.com