Apparatus for rapid and accurate installation of wall siding planks in interlocking relationship
a technology of interlocking relationship and apparatus, which is applied in the direction of roof covering, roofing using tiles/slates, roofs, etc., can solve the problems of difficult to achieve, prior art cannot make very much use of every joint, and drive up the cost of siding plank installation, etc., to achieve the effect of safe, accurate, and quick installation of siding
- Summary
- Abstract
- Description
- Claims
- Application Information
AI Technical Summary
Benefits of technology
Problems solved by technology
Method used
Image
Examples
Embodiment Construction
[0043] The purpose of this invention is for providing a series of apparatus which can be used in conjunction with the installation of siding, over walls composed of spaced apart studs, in overlapping relationship by relatively few workers in a very rapid, safe and accurate manner, without regard for where the studs are located as it relates to forming joints. This invention also allows the formation of factory created joints with unions at any location which may occur even over the space between the studs and yet create an interlocking relationship of the various apparatus of this invention and the siding planks used for creating the walls. Therefore this invention relates to creating a finished wall of siding planks with good aesthetics and resistance to high wind and storms because of its interlocking properties, and it is also achieved without having to use fasteners, such as nails, being driven into the apparatus of this invention, but only into the planks of siding itself.
[0044...
PUM
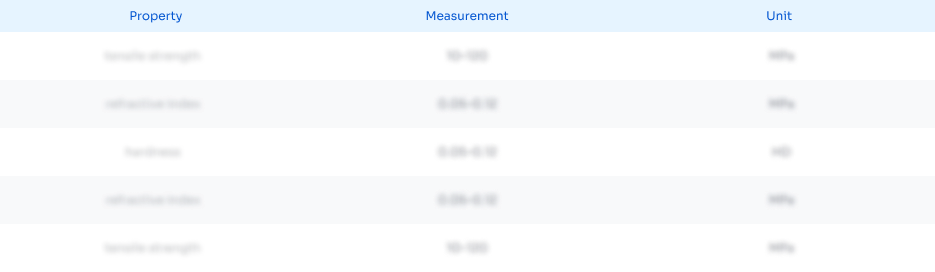
Abstract
Description
Claims
Application Information

- R&D
- Intellectual Property
- Life Sciences
- Materials
- Tech Scout
- Unparalleled Data Quality
- Higher Quality Content
- 60% Fewer Hallucinations
Browse by: Latest US Patents, China's latest patents, Technical Efficacy Thesaurus, Application Domain, Technology Topic, Popular Technical Reports.
© 2025 PatSnap. All rights reserved.Legal|Privacy policy|Modern Slavery Act Transparency Statement|Sitemap|About US| Contact US: help@patsnap.com