Hydrocarbon gas processing
a technology of hydrocarbon gas and processing equipment, applied in the direction of liquefaction, gaseous mixture working up, lighting and heating equipment, etc., can solve the problem of not having the means available to reduce the power consumption of compressors
- Summary
- Abstract
- Description
- Claims
- Application Information
AI Technical Summary
Problems solved by technology
Method used
Image
Examples
example 2
[0061] FIG. 3 represents the preferred embodiment of the present invention for the temperature and pressure conditions shown because it typically provides the simplest plant arrangement for a given C.sub.3 component recovery level. A slightly more complex design that maintains the same C.sub.3 component recovery with lower utility consumption can be achieved using another embodiment of the present invention as illustrated in the FIG. 4 process. The feed gas composition and conditions considered in the process presented in FIG. 4 are the same as those in FIGS. 1 and 3. Accordingly, FIG. 4 can be compared with the FIG. 1 process to illustrate the advantages of the present invention, and can likewise be compared to the embodiment displayed in FIG. 3.
[0062] In the simulation of the FIG. 4 process, the feed gas cooling and expansion scheme is much the same as that used in FIG. 3. The difference lies in the manner in which the vapor distillation stream 36 leaving the overhead of deethaniz...
example 3
[0068] A third embodiment of the present invention is shown in FIG. 5, wherein a different method of implementing the second mechanical-compression refrigeration cycle is applied to the present invention. The feed gas composition and conditions considered in the process illustrated in FIG. 5 are the same as those in FIGS. 1, 3, and 4. Accordingly, FIG. 5 can be compared with the FIG. 1 process to illustrate the advantages of the present invention, and can likewise be compared to the embodiments displayed in FIGS. 3 and 4.
[0069] In the simulation of the FIG. 5 process, inlet gas enters the plant at 80.degree. F. [27.degree. C.] and 1215 psia [8,377 kPa(a)] as stream 31. The feed stream 31 is cooled in exchanger 10 by heat exchange with cool residue gas at -70.degree. F. [-57.degree. C.] (stream 34a), with cool vapor at -49.degree. F. [-45.degree. C.] (stream 41a), and with separator / absorber liquids at 112.degree. F. [-80.degree. C.] (stream 35a). The cooled stre 31a (a dense-phase f...
example 4
[0079] A slightly more complex design than the FIG. 5 embodiment that maintains the same C.sub.3 component recovery with lower utility consumption can be achieved using another embodiment of the present invention as illustrated in the FIG. 6 process. The feed gas composition and conditions considered in the process presented in FIG. 6 are the same as those in FIGS. 1 and 5. Accordingly, FIG. 6 can be compared with the FIG. 1 process to illustrate the advantages of the present invention, and can likewise be compared to the embodiment displayed in FIG. 5.
[0080] In the simulation of the FIG. 6 process, the feed gas cooling and expansion scheme is much the same as that used in FIG. 5. The difference lies in the manner in which the vapor distillation stream 36 leaving the overhead of deethanizer 17 is used to generate reflux for deethanizer 17 and separator / absorber 15. Referring to FIG. 6, the deethanizer overhead vapor (stream 36) exits deethanizer 17 at -39.degree. F. [-40.degree. C.]...
PUM
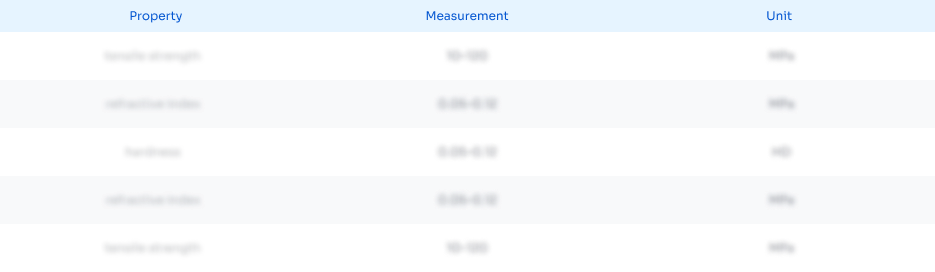
Abstract
Description
Claims
Application Information

- R&D
- Intellectual Property
- Life Sciences
- Materials
- Tech Scout
- Unparalleled Data Quality
- Higher Quality Content
- 60% Fewer Hallucinations
Browse by: Latest US Patents, China's latest patents, Technical Efficacy Thesaurus, Application Domain, Technology Topic, Popular Technical Reports.
© 2025 PatSnap. All rights reserved.Legal|Privacy policy|Modern Slavery Act Transparency Statement|Sitemap|About US| Contact US: help@patsnap.com