Soft polishing disc with holes and method of manufacturing the same
a technology of polishing disc and hole, which is applied in the field of polishing disc, can solve the problems of reducing the ability of the disc, and reducing the wear resistance of the dis
- Summary
- Abstract
- Description
- Claims
- Application Information
AI Technical Summary
Problems solved by technology
Method used
Image
Examples
example 2
[0055] A sand paper #400 composed of a paper of 1.5 mm thick was used for abrasive pieces. Each of discs was manufactured in such a manner that 80 abrasive pieces were prepared and radially disposed, and ventilation holes each having a diameter of 4 mm were alternately formed perfectly passing through an abrasive member and a back sheet at positions near to the outer circumstance of the ring portion and at positions near to the inner circumference thereof so that intervals of 15 mm were secured between the nearest ventilation holes, and a test was carried out using the disc. The other conditions of the test were set similarly to those of the example 1. Table 1 shows a result of the test.
example 3
[0056] A sand paper #1000 composed of a paper of 1.5 mm thick was used for abrasive pieces. Each of disks were manufactured in such a manner that 80 abrasive pieces, which were a little smaller than those of the example 1 with a lateral length of 15 mm and a lengthwise length of 15 mm were prepared and radially disposed, and ventilation holes each having a diameter of 5 mm were alternately formed perfectly passing through an abrasive member and a back sheet at positions near to the outer circumstance of the ring portion and at positions near to the inner circumference thereof so that intervals of 20 mm were secured between the nearest ventilation holes. Then, a test was carried out using the discs. The other conditions were set similarly to those of the example 1. Table 1 shows a result of the test.
PUM
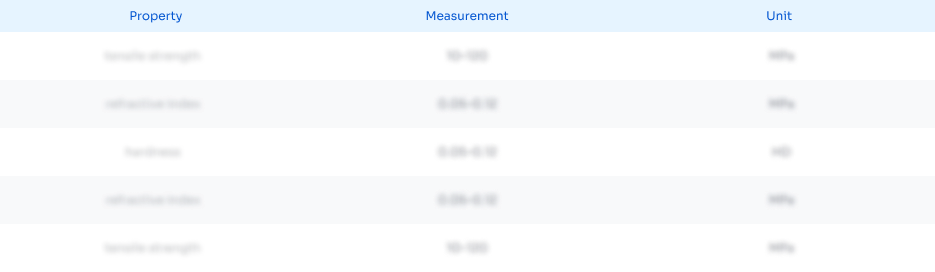
Abstract
Description
Claims
Application Information

- R&D
- Intellectual Property
- Life Sciences
- Materials
- Tech Scout
- Unparalleled Data Quality
- Higher Quality Content
- 60% Fewer Hallucinations
Browse by: Latest US Patents, China's latest patents, Technical Efficacy Thesaurus, Application Domain, Technology Topic, Popular Technical Reports.
© 2025 PatSnap. All rights reserved.Legal|Privacy policy|Modern Slavery Act Transparency Statement|Sitemap|About US| Contact US: help@patsnap.com