Golf club head and method of manufacturing the same
a golf club and head technology, applied in the field of golf club head, can solve the problems of insufficient display of characteristic features inherent in materials, increased manufacturing costs for processing and molds, and unsuitable mass production of machining
- Summary
- Abstract
- Description
- Claims
- Application Information
AI Technical Summary
Benefits of technology
Problems solved by technology
Method used
Image
Examples
first embodiment
[0046] [First Embodiment]
[0047] [Constitution of First Embodiment]
[0048] Referring to the FIGS. 1A to 1E, a constitution of a golf club head according to a first embodiment of the present invention will be described. FIGS. 1A to 1E show a golf club head of the first embodiment, which is a golf club head of a metal wood, and its members.
[0049] The golf club head 10 of the first embodiment is fabricated in such a manner that a face portion 11 is joined to an opening 19a of a body portion 19 made of stainless steel or titanium by welding or the like method.
[0050] The face portion 11 is formed by press-forming a metal plate having a thickness of 2.8 mm into a predetermined shape, the metal plate being made of stainless steel alloy, titanium alloy or the like metal.
[0051] As shown in FIG. 1B, on a front surface 11a, score lines 12 are formed by means of die sinking (i.e., processing of shaping and / or engraving a target material) of electrical discharge machining (hereinafter, die sinking...
second embodiment
[0069] [Second Embodiment]
[0070] [Constitution of Second Embodiment]
[0071] Referring to FIGS. 2A to 2E and FIG. 3, a constitution of a golf club head according to a second embodiment of the present invention will be described. FIGS. 2A to 2E show a golf club head of the second embodiment, which is a golf club head of an iron, and FIG. 3 shows the golf club head seen from the rear side.
[0072] As shown in FIG. 2A, the golf club head 20 is fabricated in such a manner that the face portion 21 is attached to the attaching portion 29a of the body 29 having a cavity back structure made of stainless steel or the like by welding or the like method.
[0073] The face portion 21 is obtained by press-forming a metal plate having a thickness of 2.4 mm into a predetermined shape, the metal plate being made of stainless steel alloy, titanium alloy, or the like metal.
[0074] As shown in FIGS. 2B and 2D, on the front surface 21a, score lines 22 are formed by electrical discharge die sinking using a sili...
third embodiment
[0092] [Third Embodiment]
[0093] [Constitution of Third Embodiment]
[0094] Referring to FIG. 4, a golf club head according to a third embodiment of the present invention will be described. FIG. 4 shows the golf club head 30 of the third embodiment, which is a golf club head of a short iron having a hollow structure.
[0095] As described in conventional art, in the short iron (for example, Pitching Wedge [PW], Approach Wedge [AW], and Sand Wedge [SW]), the hitting sensation and the hitting direction are important.
[0096] In the short iron, the approaching performance is also important. Here, the approaching performance is composed of two performances of allowing an actual hit distance to be as close as an estimated hit distance and of causing the hit ball to stop as close as possible to the point where the ball has fallen down. The approaching performance is important in the short iron because the short iron is used at a short play in which the pin (the pole with a flag standing in the ho...
PUM
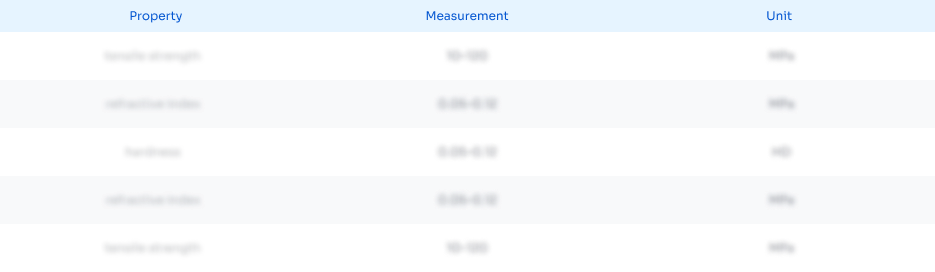
Abstract
Description
Claims
Application Information

- R&D
- Intellectual Property
- Life Sciences
- Materials
- Tech Scout
- Unparalleled Data Quality
- Higher Quality Content
- 60% Fewer Hallucinations
Browse by: Latest US Patents, China's latest patents, Technical Efficacy Thesaurus, Application Domain, Technology Topic, Popular Technical Reports.
© 2025 PatSnap. All rights reserved.Legal|Privacy policy|Modern Slavery Act Transparency Statement|Sitemap|About US| Contact US: help@patsnap.com