Vibration sensor based on magnetic suspension principle
A vibration sensor and magnetic levitation technology, applied in the direction of instruments, electromagnetic means, seismic signal receivers, etc., can solve the problems of narrow detection frequency band, large noise interference, insufficient detection of broadband elastic waves, etc., and achieve the effect of high sensitivity
- Summary
- Abstract
- Description
- Claims
- Application Information
AI Technical Summary
Problems solved by technology
Method used
Image
Examples
Embodiment Construction
[0020] Based on the above magnetic levitation principle, we built more than 300 one-dimensional magnetic levitation vibration sensors, and measured the amplitude-frequency characteristics of the sensors. The results are shown in Figure 3. The constructed magnetic levitation vibration sensor was used in petroleum geophysical prospecting in a certain place in Jiangsu, and a single shot comparison experiment was carried out with a single magnetic levitation sensor and 24 traditional moving coil geophones imported from France. The results are shown in Figure 4, left The picture shows the result of a single magnetic levitation vibration sensor, and the picture on the right shows the combined result of 24 traditional moving coil detectors. It can be seen that the resolution of the magnetic levitation sensor used in petroleum geophysical exploration is higher than that of the combination of traditional moving coil detectors. Fig. 5 is a spectrum diagram of the reflected wave signal r...
PUM
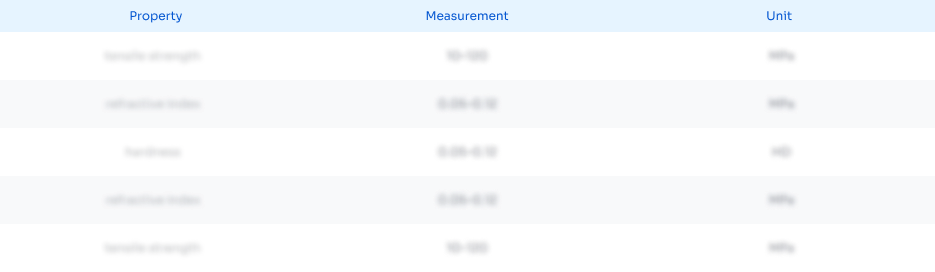
Abstract
Description
Claims
Application Information

- Generate Ideas
- Intellectual Property
- Life Sciences
- Materials
- Tech Scout
- Unparalleled Data Quality
- Higher Quality Content
- 60% Fewer Hallucinations
Browse by: Latest US Patents, China's latest patents, Technical Efficacy Thesaurus, Application Domain, Technology Topic, Popular Technical Reports.
© 2025 PatSnap. All rights reserved.Legal|Privacy policy|Modern Slavery Act Transparency Statement|Sitemap|About US| Contact US: help@patsnap.com