Oriented silicon steel insulation coating capable of improving punched piece performance
A technology of oriented silicon steel and insulating coating, applied in the direction of coating, etc., can solve the problems of limited production and application, small degree of improvement in shear performance, poor heat resistance of coating, etc.
- Summary
- Abstract
- Description
- Claims
- Application Information
AI Technical Summary
Problems solved by technology
Method used
Image
Examples
Embodiment Construction
[0049] Refer to Table 3 and Table 4 for specific embodiments.
[0050] It can be seen from Table 4 that in practical examples 1 to 8, as the amount of polyether-modified silicone oil added increased, the number of punching times increased significantly, up to 300,000 times. However, in Comparative Examples 1 and 3, since no organic silicon component was added to the coating solution, the number of punching times of the oriented silicon steel sheet coated with pure inorganic coating was only 15,000. Of course, the more polyether-modified silicone oil is added, the better. For example, in Comparative Examples 2 and 4, although more organic components increased the number of punching times to 450,000, it caused the appearance of the coating to deteriorate.
[0051] In the implementation of the present invention, a roll coater is used to apply the coating solution to the cold-rolled electrical steel substrate for baking and high-temperature sintering, so it can be popularized and ...
PUM
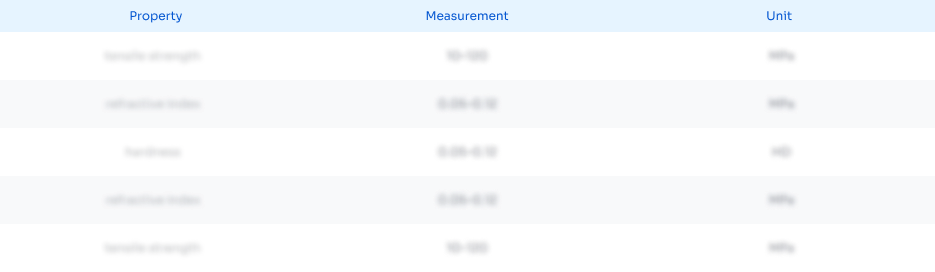
Abstract
Description
Claims
Application Information

- R&D Engineer
- R&D Manager
- IP Professional
- Industry Leading Data Capabilities
- Powerful AI technology
- Patent DNA Extraction
Browse by: Latest US Patents, China's latest patents, Technical Efficacy Thesaurus, Application Domain, Technology Topic, Popular Technical Reports.
© 2024 PatSnap. All rights reserved.Legal|Privacy policy|Modern Slavery Act Transparency Statement|Sitemap|About US| Contact US: help@patsnap.com