SO3 gas jetting sulfonation reactor and process
A technology of sulfonation reactor and gas injection, which is applied in chemical/physical/physicochemical nozzle reactors, chemical methods for reacting liquid and gaseous media, chemical instruments and methods, etc. High cost, over-sulfonation and other problems, to achieve the effect of flexible and simple operation, convenient raw material switching, and stable product quality
- Summary
- Abstract
- Description
- Claims
- Application Information
AI Technical Summary
Problems solved by technology
Method used
Image
Examples
Embodiment 1
[0021] Embodiment 1: Sulfonation of dodecylbenzene
[0022] SO 3 The gas jet sulfonation reactor is composed of a nozzle and a reactor body. The nozzle is composed of a gas nozzle 3, a liquid distribution chamber 4, an atomization nozzle 5, a liquid phase raw material inlet 1 and a mixed gas inlet 2. The gas nozzle 3 and The mixed gas inlet 2 communicates with and is fixed on the top of the liquid distribution chamber 4, the liquid phase raw material inlet 1 is located at the lower part of the side of the liquid distributor 4, the atomizing nozzle 5 is fixed in the liquid distribution chamber 4, and the lower part of the gas nozzle 3 enters the atomizing nozzle 5 , the top of the atomizing nozzle 5 is open, the position of the top of the atomizing nozzle 5 in the liquid distribution chamber 4 is higher than the position of the liquid phase raw material inlet 1 in the liquid distribution chamber 4, the nozzle is fixed on the top of the reactor body 7, and the mist The lower pa...
Embodiment 2
[0024] Embodiment 2: the sulfonation of toluene
[0025] Toluene (average molar mass: 92) is continuously converted from SO at a flow rate of 5.8kg / h at 5°C to 10°C 3 The liquid phase inlet 1 of the gas jet sulfonation reactor enters the liquid distribution chamber 4, then overflows into the atomizing nozzle 5 through the top of the atomizing nozzle 5, and then flows downward along the inner wall of the atomizing nozzle 5, SO 3 / air (volume ratio 6%) mixed gas by SO at 55°C 3 The gas phase inlet 2 of the gas injection sulfonation reactor enters the gas nozzle 3, and the gas velocity ejected from the gas nozzle 3 is 218m / s, SO 3 / alkylbenzene feed molar ratio 1.03:1, SO 3 / Air mixed gas is in contact with the organic material and is sprayed from the atomizing nozzle 5 into the reactor body 7 for reaction. The reaction time in the reactor body 7 is 1 second, and the obtained sulfonation reaction product and unreacted SO 3 / air mixture from SO 3 After the product outlet 8 of ...
Embodiment 3
[0026] Example 3: Sulfation of polyoxyethylene lauryl ether (n=3)
[0027] Lauryl alcohol polyoxyethylene ether (n=3, hereinafter referred to as AEO 3 , average molar mass 326) at a flow rate of 16.3kg / h at 32°C continuously from SO 3 The liquid phase inlet 1 of the gas jet sulfonation reactor enters the liquid distribution chamber 4, then overflows into the atomizing nozzle 5 through the top of the atomizing nozzle 5, and then flows downward along the inner wall of the atomizing nozzle 5, SO3 / air (volume ratio 3.5%) mixed gas by SO at 55°C 3 The gas phase inlet 2 of the gas injection sulfonation reactor enters the gas nozzle 3 and the gas velocity ejected from the gas nozzle 3 is 195m / s, SO 3 / alkylbenzene feed molar ratio 1.03:1, SO 3 / Air mixed gas is in contact with the organic material and is sprayed into the reactor body 7 from the atomizing nozzle 5 to react. The reaction time in the reactor body 7 is 3 seconds, and the obtained sulfonation reaction product and unrea...
PUM
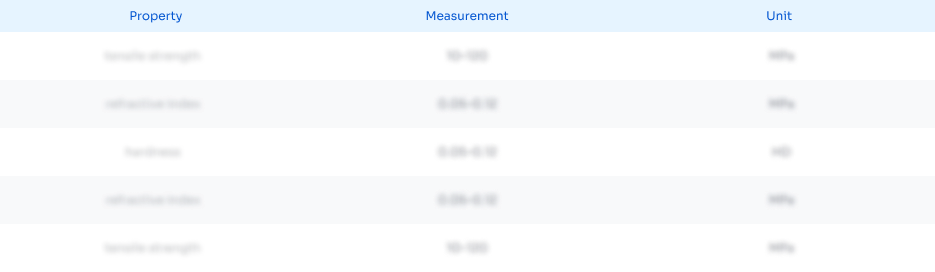
Abstract
Description
Claims
Application Information

- R&D
- Intellectual Property
- Life Sciences
- Materials
- Tech Scout
- Unparalleled Data Quality
- Higher Quality Content
- 60% Fewer Hallucinations
Browse by: Latest US Patents, China's latest patents, Technical Efficacy Thesaurus, Application Domain, Technology Topic, Popular Technical Reports.
© 2025 PatSnap. All rights reserved.Legal|Privacy policy|Modern Slavery Act Transparency Statement|Sitemap|About US| Contact US: help@patsnap.com