Digital control method for spiral pressure machine transmission and digital control spiral pressure machine
A screw press, industrial control technology, applied in the direction of press, punching machine, computer control, etc., can solve the problems of fragility, complex control circuit, difficult to popularize, etc., to extend the life of the mold, high forming accuracy, and simplify the structure. Effect
- Summary
- Abstract
- Description
- Claims
- Application Information
AI Technical Summary
Problems solved by technology
Method used
Image
Examples
Embodiment 1
[0024] As shown in Figure 1, the switched reluctance speed regulating motor 1 is installed on the fuselage 13, the output shaft is connected with the flywheel 2 through the coupling 18, the screw rod 5 is located at the central axis of the fuselage 13 and is installed on the fuselage through the bearing 4 13, the upper end of the screw rod 5 is connected with the flywheel 2 as a whole, the screw rod 5 and the nut 6 cooperate with the screw pair, the nut 6 and the slider 7 are connected as a whole, and the guide rail 8 is installed symmetrically with the central axis in the fuselage 13, and the guide rail 8 and the slider The block 7 is slidably fitted, the force sensor 10 is installed in the workbench 9, the infrared pyroelectric sensor 12 is installed on the fuselage 13 in the dangerous area of operation, the brake 3 is fixed on the fuselage 13, and its brake block is hugged on the flywheel 2 .
[0025] As shown in Figure 2, the industrial control microcomputer is connected...
Embodiment 2
[0030] As shown in Figure 4, in the CNC screw press of the present invention, the switched reluctance speed regulating motor 1 is installed on the body 13, and the output shaft of the switched reluctance speed regulating motor 1 is connected with the pinion 19 through a shaft coupling 18, and the pinion 19 meshes with the flywheel 2, the upper end of the screw 5 is connected with the flywheel 2 as a whole, the screw 5 and the nut 6 cooperate with a screw pair, the nut 6 and the slider 7 are connected as a whole, and the guide rail 8 is installed symmetrically with the central axis in the fuselage 13, The guide rail 8 is slidably matched with the slider 7, the load cell 10 is installed in the workbench 9, the infrared pyroelectric sensor 12 is installed on the fuselage 13 in the dangerous area of operation, the brake 3 is fixed on the fuselage 13, and its brake block is held On the brake pads of flywheel 2.
Embodiment 3-4
[0032] As shown in Figure 5-6, the change of the screw press is mainly in the transmission mechanism. For example, in Figure 5, the output shaft of the switched reluctance speed regulating motor 1 is connected with the flywheel 2 through the coupling 18, and the screw 5 is connected with the flywheel 2 as In one piece, the screw 5 is installed on the fuselage 13 through the thrust bearing 4, the screw 5 and the nut 6 cooperate with a screw pair, the nut 6 and the wedge 20 are connected as one, and the wedge 20 and the slider 7 slide and fit through the dovetail slideway. A guide rail 8 is installed in the fuselage 13, and the guide rail 8 is slidably matched with the slide block 7. The load cell 10 is installed in the workbench 9, the infrared pyroelectric sensor 12 is installed on the fuselage 13 in the operation danger zone, and the brake 3 is fixed on the machine. On the body 13, its brake block is hugged on the brake pad of flywheel 2. When the screw rod 5 rotates, the nut...
PUM
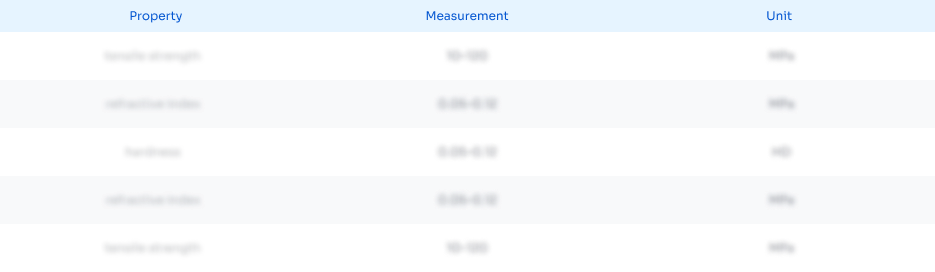
Abstract
Description
Claims
Application Information

- R&D Engineer
- R&D Manager
- IP Professional
- Industry Leading Data Capabilities
- Powerful AI technology
- Patent DNA Extraction
Browse by: Latest US Patents, China's latest patents, Technical Efficacy Thesaurus, Application Domain, Technology Topic, Popular Technical Reports.
© 2024 PatSnap. All rights reserved.Legal|Privacy policy|Modern Slavery Act Transparency Statement|Sitemap|About US| Contact US: help@patsnap.com